Products made of silicone rubber must be produced with the highest level of efficiency possible. There are several procedures that can satisfy the fabricant's demands. Here, the benefits and drawbacks of injection molding and transfer molding are contrasted.
Moldeo por inyección
What is Injection Molding?
injection molding is a molding procedure that is distinguished by the use of injection technology. Because raw material is injected into a mold cavity, it is known as "injection molding." A screw pushes the material into a hopper during the injection molding process. The substance is heated before being put into the cavity of the mold. Compression molding and injection molding both employ heat and pressure to create their finished products. Injection molding and compression molding both transport the material via hoppers and screws, however injection molding does not.
Injection Molding Process
Here is how the procedure for injection molding works:
- A heated barrel is used to feed the material, which is frequently in the form of pellets or granules, and heat it to a molten condition.
- A reciprocating screw or ram injector forces the liquid material into the mold cavity and into a path known as a sprue.
- The melt is kept inside the mold and either heated to cure (for thermoplastics) or cooled to harden it (termoestables).
- Until the substance has hardened, the mold is opened and the element is ejected.
Injection Molding Advantages
For both silicone and plastic goods, injection molding is the most economical molding technique. This technology offers special benefits.
- Perfect Materials: Liquid thermosets or molten thermoplastics can readily flow into mold cavities. Faster cavity filling and quick cure are the results.
- Greater Capacity: Because injection molding machines can fit more cavities into a single mold, more units can be produced during each manufacturing cycle.
- Minimal Waste: Because the sprues are smaller and there are no overflow channels, there is less material waste as compared to transfer molding and other molding techniques.
- Rapid: The typical injection molding cycle time ranges from 2 seconds to 2 minutes. Compared to other molding techniques, this is quicker.
Injection Molding Disadvantages
The following are some drawbacks of injection molding as opposed to compression molding:
- High injection pressures for plastic are necessary for injection molding. In order to endure these intense pressures, the mold must be constructed. The tooling now costs more as a result.
- Making huge, thin items like automobile panels with injection molding is not a good idea.
Common Materials of Injection Molding
Injection molding is suitable for both thermoplastic and thermosetting materials, the common materials include:
- Goma de silicona líquida (LSR)
- Poliestireno (PD)
- Poliamida (PA)
- Polietileno (PE)
- Cloruro de polivinilo (CLORURO DE POLIVINILO)
- Acrylonitrile Butadiene Styrene (ABS)
- polipropileno (PÁGINAS)
Moldeo por transferencia
¿Qué es el moldeo por transferencia?
El moldeo por transferencia es el método de crear componentes en un molde cerrado utilizando materiales termoendurecibles que se empujan a través de canales y compuertas hacia la cavidad o cavidades cerradas bajo presión y en un ambiente caliente., condición plástica de una cámara auxiliar conocida como recipiente de transferencia.
Proceso de moldeo por transferencia
El método de moldeo por transferencia es exactamente como el moldeo por inyección., con algunas excepciones clave. Following are the steps:
- El material se coloca en una cámara de retención conocida como recipiente de transferencia., que puede o no haber sido calentado.
- El material es empujado hacia la cavidad del molde por un émbolo que es impulsado hidráulicamente a través de un tubo conocido como bebedero..
- La sustancia se mantiene dentro del molde y se calienta para curar las aleaciones metálicas o se enfría para endurecer los termoplásticos. (termoestables). Cualquier material que todavía esté dentro del bebedero después de que el elemento se endurezca se vincula a él..
- Once the material has set, se abre el molde, y la pieza es expulsada.
- The sprue's extra material is taken out.
Ventajas del moldeo por transferencia
The preheating of the material and injection through a small aperture increase the temperature distribution inside the material and speed up the crosslinking process, which is one of transfer molding's benefits.
- Formación mínima de rebabas en las líneas de partición de los moldes.
- Tiempos de configuración más rápidos.
- Menores costos de herramientas.
- Mayor flexibilidad en el diseño de piezas (y capacidad para la complejidad de la pieza).
Desventajas del moldeo por transferencia
El moldeo por transferencia tiene algunos inconvenientes debido a su facilidad de uso y velocidad.:
- Residuos de materiales: Debido al mayor tamaño de los bebederos y canales de rebose, el moldeo por transferencia genera desperdicio de material adicional.
- Producción lenta: Transfer molding's production pace is slower than injection molding because materials must be heated prior to molding.
- Cantidad baja: Las máquinas de moldeo por transferencia crean menos piezas por ciclo que las máquinas de moldeo por inyección porque no pueden manejar muchas cavidades.
Materiales poliméricos comunes de moldeo por transferencia
El moldeo por transferencia puede aplicar materiales termoestables y termoplásticos, Los materiales poliméricos más comunes incluyen:
- Poliéster insaturado
- Epoxy
- Plásticos de fenol-formaldehído
- Goma de silicona
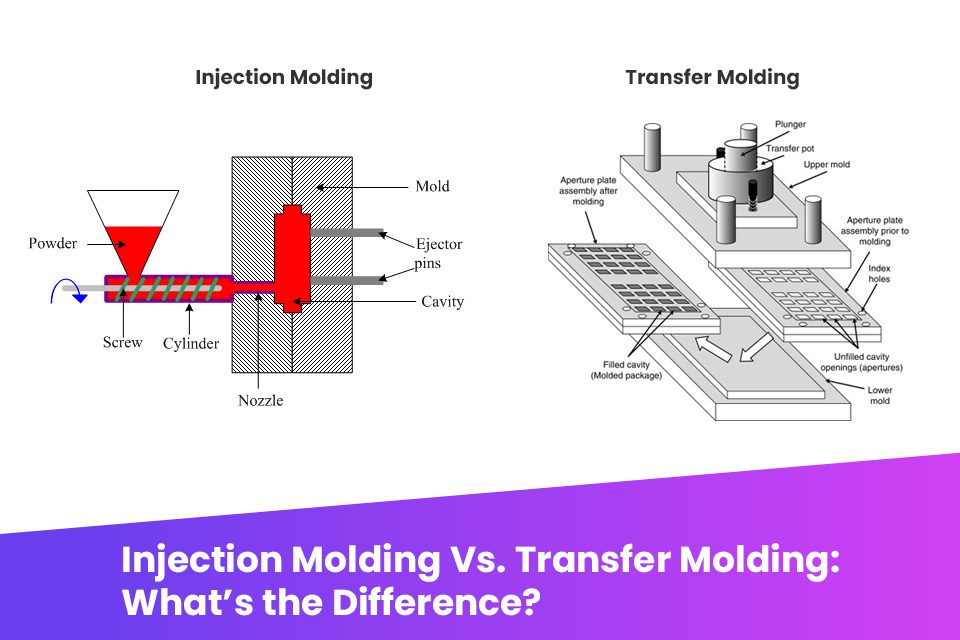
Moldeo por inyección versus moldeo por transferencia: Cual es la diferencia?
The procedures are where these two moldings diverge most. Transfer molding and injection molding use plungers to drive materials into the molds, respectivamente.
There are several distinctions between injection molding and transfer molding that affect how final goods are produced. The following are the most important distinctions to take into account:
Molding Method Selection
There are a number of considerations we should address when deciding which molding technique is best for fabricating parts.
- A different type of machinery is used in transfer molding to provide pressure to the piston; this press is less expensive than an injection molding equipment. Transfer molding requires less money up front as a result. Small and medium-sized items are better suitable for transfer molding since the press produces less pressure than an injection molding machine.
- Cavitation Limitation: The press or injection molding machine's capacity determines how much cavitation may occur in a mold. The injection molding machine often has larger cavity space. Como resultado, the cost per unit will drop and high-volume production will run more smoothly.
- Preparation of Raw Materials: In injection molding, we have ready access to raw materials (compounds A and B). Prior to inserting the raw materials in pots, we must prepare them in a number of procedures for transfer molding. This will lengthen the transfer molding process cycle time and ultimately raise the cost of production.
- Residuos de materiales: Transfer molding produces more waste than injection molding because of bigger sprue, more air holes, and overflow grooves. Además, additional processes including trimming, cryogenic tumbling, and precise grinding are required to eliminate these wastes.
Moldeo por inyección versus moldeo por transferencia: Which Is Better For Your Product?
Although injection molding and transfer molding share many similarities, their differences are crucial in determining which method is best for producing a specific product. The following are the most important differences to consider when deciding which method to use:
Initial Investment
Both processes require a toolmaker or machinist to build molds, which is an expensive process. Sin embargo, the cost of the machinery involved is the biggest factor in determining startup costs. The injection molding machine is significantly more expensive than the press needed for transfer molding, primarily because of the complexity and specialization of the components within the machine.
It also takes much more time to set up compared to a transfer mold machine, which means it will take longer for a project to get underway. The cost and complexity also mean that maintenance costs are substantially higher for injection molding machines.
Speed Of Production
Injection molding has a very short process cycle, running anywhere from two seconds to two minutes, depending on the size of the product. The overall production time increases with the removal of any excess material, such as flash or the sprue, but is still much shorter than the production time for transfer molding. The primary disadvantage in transfer molding is that the material is prepared before placement in the machine, increasing the time of the cycle significantly.
Cost Of Production
Cost of production does not typically favor one method over the other in all cases, but instead depends on the geometry of the product. Materials requiring a high injection pressure would require a more powerful injection machine, meaning it would be more expensive to use an injection machine instead of a transfer machine.
The same can be said for a larger part. Sin embargo, injection machines can accommodate more cavities, increasing the production per cycle. Injection molding also involves more automation than transfer molding machines, meaning long-term labor costs are reduced significantly for high-quantity projects.
Product Shape And Accuracy
Both processes allow for impressive accuracy, and both provide very consistent results. Sin embargo, injection molding doesn’t handle sharp edges very well and can end up rounding off edges that were meant to be sharp. Además, even though both processes can produce units with very complex forms, the cost of doing so with transfer molding is significantly lower than with injection molding, primarily because complex injection molds require more intricate and expensive injection systems to produce.
Amount Of Waste
Although flash and sprue waste does happen with injection molds, transfer molding produces much more waste on average. This is primarily due to the presence of a wider sprue, air holes, and overflow grooves that are not present in injection molds. If the material involved is thermosetting, this can result in substantial material waste.
Product Size
Both of these methods operate well for small- to medium-sized products, but injection molding has the capacity to create much larger products, up to 80 square feet. Transfer molding is best suited to small and medium part sizes, primarily due to limitations in press sizes.
Product Volume
Injection molding is much better suited to higher quantities of larger, thin-walled parts, while transfer molding is better suited to encasements and small quantities of simpler molds.
In terms of the quantity of products desired, injection molding is vastly superior to transfer molding. The relatively automated systems, combined with faster cycle times, make this method much more cost-effective in the long run for high-volume projects.
We summarize the main information of liquid silicone injection molding vs transfer molding as following
— disadvantage, + advantage
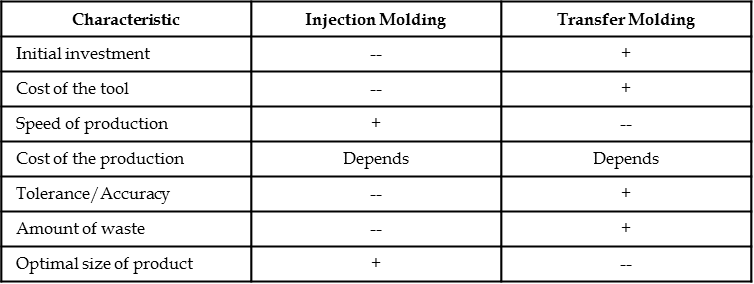
Transfer Molding Vs Injection Molding FAQs
What is transfer Moulding used for?
Moldeo por transferencia, which differs slightly from conventional compression molding, is frequently used for thermoset materials. It combines the processes of compression molding and injection molding. In this procedure, a holding chamber known as the pot is used to preheat the polymer.
What is the difference between compression transfer and injection moulding?
Compression molding is more suited to pliable and flexible materials, while injection molding is better suited to big volume production. Además, tooling costs for compression molding are lower.
What is another name for transfer Moulding?
Similar to compression molding, transfer molding (BrE molding) involves measuring and inserting the proper amount of the molding compound, which is often a thermoset plastic, prior to the molding process. The molding compound is heated beforehand and loaded into the "pot," a chamber.
What products are made by transfer molding?
Manufacturers can encase components like integrated circuits, enchufes, connections, pins, bobinas, and studs using transfer molding. Transfer molding can produce materials with electronics, ceramic, or other inserts in addition to metal inserts.
¿Cuáles son los cuatro tipos de molduras??
Conclusión
There are a number of elements to consider when choosing the optimal method for producing a given product. As was already noted, before injecting or transferring the polymer to create the pieces, both transfer molding and injection molding allow the introduction of inserts (metal, fibers, or ceramic) in the cavity. The equipment utilized for each procedure varies, though. While an injection molding machine is used for injection molding, a press applies pressure to the piston during transfer molding. The initial expenditure for transfer molding is lower since a press is less expensive than an injection molding machine. Also, because transfer molding does not need more complicated systems, such the intricate expulsion system used in injection molding, the cost of the mold is lower. Debido a esto, transfer molding maintenance expenses are also lower.
Although both methods are capable of creating items with intricate geometries, injection molding machines often have more cavity space, which lowers unit costs and increases efficiency. Transfer molding is less advantageous than injection molding in several ways, though. Por ejemplo, transfer molding requires that the material be ready before going into the pot, which extends processing time and raises production costs. Además, wider sprues, air holes, and overflow grooves in transfer molding result in more waste. Further procedures including cutting, cryogenic, tumbling, and precise grinding are used to remove this waste.
En conclusión, both injection and transfer molding processes can produce high-quality products in similar ways. Sin embargo, injection molding is better suited for parts that require precise intricacies and consistency, while transfer molding is better suited for simpler molds with faster tool builds.