Depuis son invention à la fin du XIXe siècle, silicone injection molding has completely changed how we make silicone goods. Although technology has advanced substantially over the years, there are still two basic kinds of injection molds: hot runner vs cold runner systems. Each of these systems has unique advantages and disadvantages that make them more suitable for particular purposes.
When choosing the best solution for your particular application, knowing the distinctions between these technologies will help you and your silicone injection specialist have a more fruitful and educated conversation.
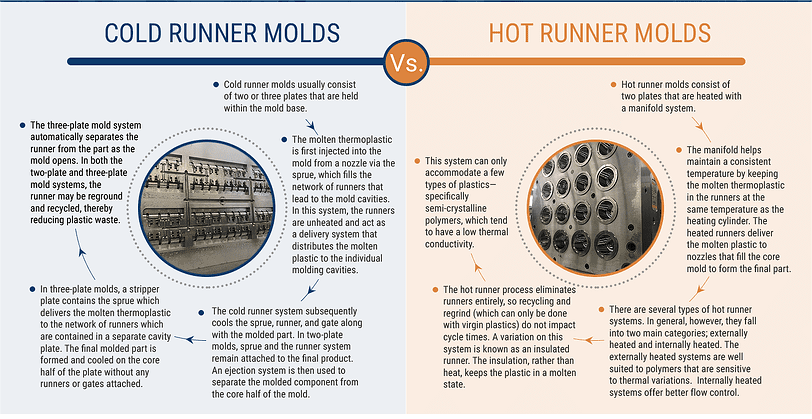
Cold Runner Mold Systems
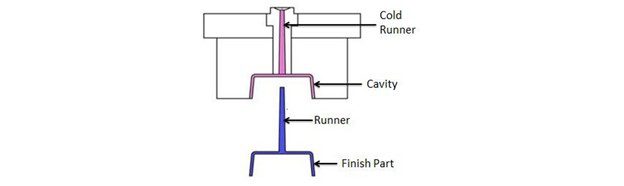
Cold runner molds often have two or three plates that are supported by the mold's base. The network of runners leading to the mold cavities are filled by the injection of molten thermoplastic into the mold from a nozzle via the sprue. In this technique, the runners serve as a delivery system that delivers the molten plastic to each individual molding cavity while remaining unheated. The sprue, runner, and gate are subsequently cooled along with the molded item via the cold runner system.

Cold Runner Mold Systems
The runner system and the sprue are still linked to the finished product in two-plate molds. The molded component is then separated from the mold's core portion using an ejection method. The runners and the pieces were not separated, for those of you who construct a model automobile at some point in your adolescence. That last step of the procedure was carried out by the kid who put the model together.
Advantages of Cold Runner
- comparatively less expensive than the hot runners they replace
- lower costs for upkeep
- handles a broad range of thermoplastics, both common and engineered
- more adaptability than hot runners
- enables quicker design changes
Disadvantages of Cold Runner
- After each run, the runner must be physically removed from the completed section.
- After each run, runners should be reground and recycled to reduce plastic material waste.
- higher cost per unit of output than hot runner systems
- Runners have to be removed
- Takes longer than a hot-runner system
How does a cold runner system work?
When molten silicone is discharged from the nozzle, it is transferred into a mold cavity via cold runners, which are unheated channels. Donc, the cold runners' channel must be wider, requiring a higher flow of silicone during each cycle. In order to get at the ideal design, you may need to shoot a lot of components and go through numerous iterations, which might increase the cost relative to a hot runner assembly method.
Hot Runner Molds Systems

A hot runner system is a collection of heated parts used in silicone injection mold cavities to inject molten plastic. The portion of the mold that is formed like the pieces to be manufactured is called the cavity.

Hot Runner Molds Systems
A heated manifold and many heated nozzles are often included in a hot runner system. The major responsibility of the manifold is to distribute the silicone coming into the mold to the numerous nozzles, who then accurately meter it to the injection locations in the cavities.
Advantages of Hot Runner
- minimizes unnecessary waste during molding
- Ideal for larger parts and higher volumes
- makes the mold automation process more effective
- Cycle Time Reduction/Lower Processing Costs
- Improved Molding System Efficiency
Disadvantages of Hot Runner
- Usually cost more than cold runner systems.
- There is a need for additional internal or exterior heating sources.
- Typiquement, the cost of tooling is more than that of cold runner systems.
- Not ideal for some heat-sensitive polymers
How does a hot runner system work?
Two heated plates make up a hot runner mold, which is heated via a manifold system. There are hot runners that are both inside and externally heated. Molds that have internal heating are the best option when more flow control is needed. Utilizing externally heated molds is the best choice when working with very heat-sensitive materials. Heat runners can be heated using a variety of techniques, including as heating rods, coils, and pipes. A hot runner system keeps materials molten throughout the runner process until the material flows into the mold cavity.
Quelle est la différence: Hot Runner vs Cold Runner Injection Molding?
When the decision has been made to incorporate a hot runner system into a mold, the question arises of what to look for. With the many independent suppliers out there, the types and choices of systems are obviously numerous and often the only resemblance of one system to another is the common term "hot runner."
Hot runner technology comes with many options and the driver of selection - in order to obtain all the molding efficiencies and part quality benefits - must be the application. There are cases where price, par exemple, has taken preference over the application with the consequence of lower than expected mold efficiency and sacrificed part performance.
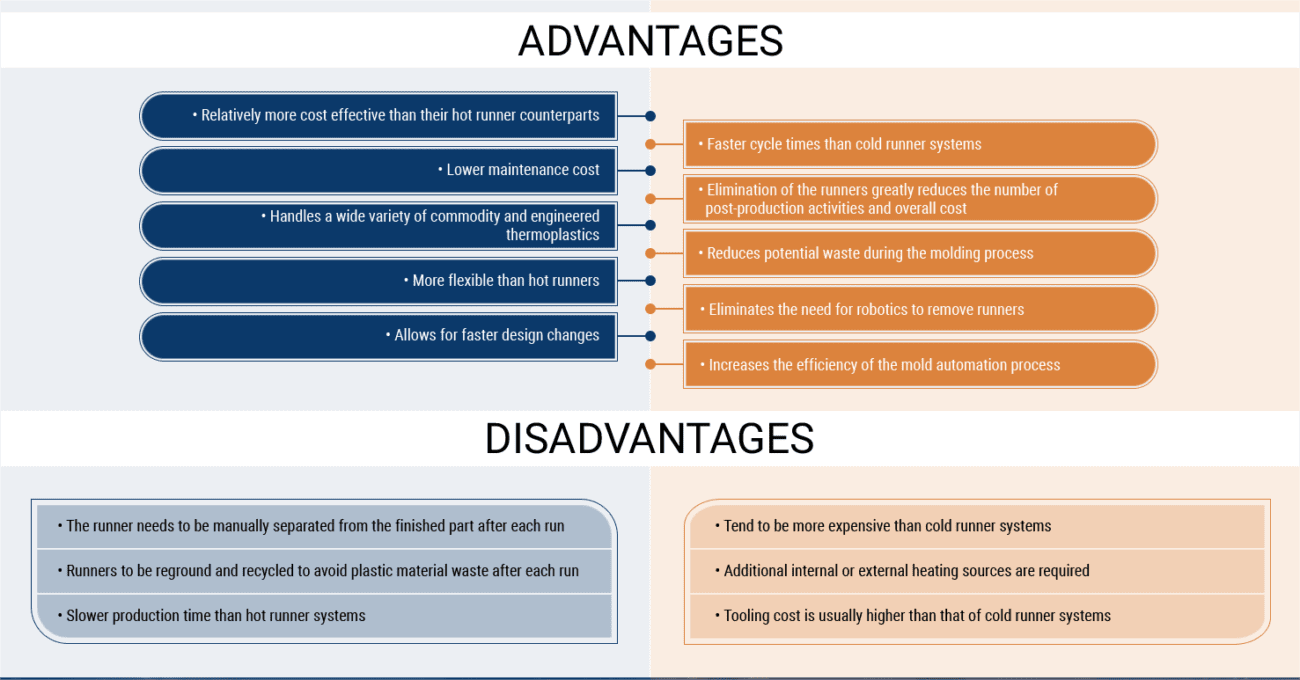
Hot Runner vs Cold Runner Mold – Considerations When Choosing Each System
Only after properly studying how they function can the two be chosen. Here are a few things to think about while selecting any molding system.
Considerations When Choosing the Hot Runner Molds
Price, delivery time, and quantity considerations should all be made while selecting the best hot runner mold. Cependant, the technological part of the runner system is what matters most. Here are a few things to remember:
- Injection Pressure
- Chauffage
- Gate Type
- Standard or Custom-Made System
- Types of Plastics Processing
- Runner Size
Consideration When Choosing the Cold Runner Mold
Below are the important factors you should consider when choosing a cold runner mold.
- Buses
- Nozzle Tips
- Runner Manifolds
- Piston Assembly
Which System is Right for You?
The optimum mold system may be obvious to you or it may be more challenging, depending on exactly what you're doing with your molds—materials, applications, size, volume, etc.. Par exemple, a cold-runner mold system is probably your best option if you solely work with heat-sensitive polymers. You're probably searching for a hot-runner mold system if you're producing in big quantities and require faster cycle times.
To learn more about hot runner vs. cold runner injection molding or to get a price, get in touch with an LGDsilicone engineer. In order to help you choose the optimal strategy for your project based on the components and materials you want to employ, we may assist you in performing a cost/benefit analysis of the various systems.
What is the purpose of a hot runner system?
Hot runners promote better part aesthetics, more flexibility, and better process monitoring while increasing productivity and system performance. They also increase energy efficiency and remove trash plastic, which leads to shorter cycle times and cheaper component costs.
Why use hot runner for injection molding?
The fact that the plastic in the runners will never harden is one of the system's main benefits. This shortens the cycle time and enables quicker processing. Because the material does not firm until the mold is filled, this approach also reduces plastic waste.
How many types of hot runners are there?
Hot runners come in two varieties: internally heated and externally heated. For heat-sensitive materials, externally heated molds are preferable, but internally heated molds offer greater flow control.