Silicone compression molding is a common method for making strong, long-lasting silicone parts. This process is cost-effective and works well in industries like automotive, medisch, consumer goods, and electronics. It has lower tooling costs than other molding methods and can produce large or thick-walled parts with excellent material properties.
This guide explains how silicone compression molding works, its advantages, limitations, and key applications. It will help manufacturers decide when and why to use this method.
What is Silicone Compression Molding?
Silicone compression molding is a process where a set amount of high-consistency silicone rubber (HCR) is placed into a mold and compressed under heat and pressure. The heat causes the silicone to cure and take its final shape.
In tegenstelling tot spuitgieten, which pushes liquid silicone into a mold under high pressure, compression molding uses direct compression. This makes it a better choice for larger, thicker parts that do not need extreme precision or complex details.
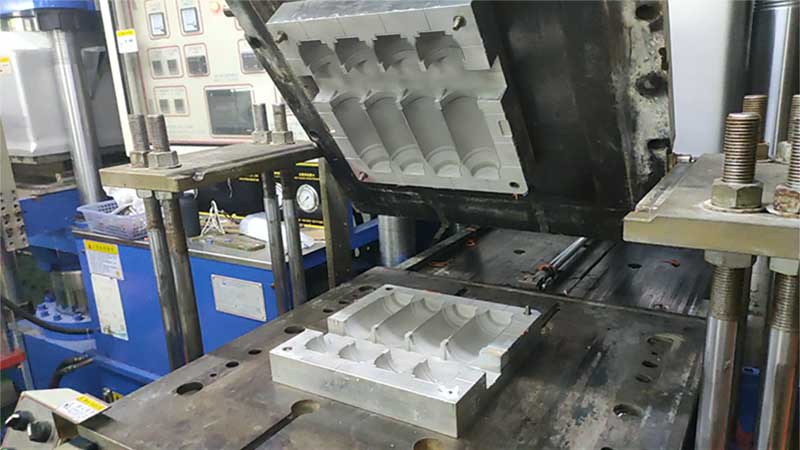
The Silicone Compression Molding Process
The silicone compression molding process consists of several key stages:
1. Mold Preparation
Before production begins, a precise mold must be created to match the desired product shape. Molds are typically made from P20 tool steel, H13 hardened steel, of 420 stainless steel, depending on the production volume and material requirements. Proper venting and mold design help to ensure uniform material distribution and prevent defects.
2. Material Preparation
Silicone compression molding uses high-consistency rubber (HCR), which is known for its excellent heat resistance, flexibiliteit, and durability. Several material properties must be considered, inbegrepen:
- Hardheid – Determines flexibility and stiffness.
- Temperatuursbestendigheid – Ranges from -55°C to 300°C, making it ideal for extreme environments.
- Tear Strength – Ensures the final product withstands mechanical stress.
3. Placing Silicone into the Mold
The pre-measured silicone compound is placed into the open mold cavity. Unlike liquid silicone rubber (LSR) used in injection molding, HCR must be manually placed into the mold before compression begins.
4. Compression and Curing
The mold is closed and subjected to high pressure, forcing the silicone to conform to the cavity’s shape. Heat is applied, initiating the vulcanization process, which transforms the uncured silicone into a solid, durable component. The exact temperature and pressure settings depend on the part thickness and material formulation.
5. Cooling and Demolding
Once cured, de mal wordt geopend, and the finished silicone part is removed. Compression molding can create extra material, called flash, around the edges. To meet final product standards, post-processing steps like trimming, deflashing, or secondary curing may be needed.
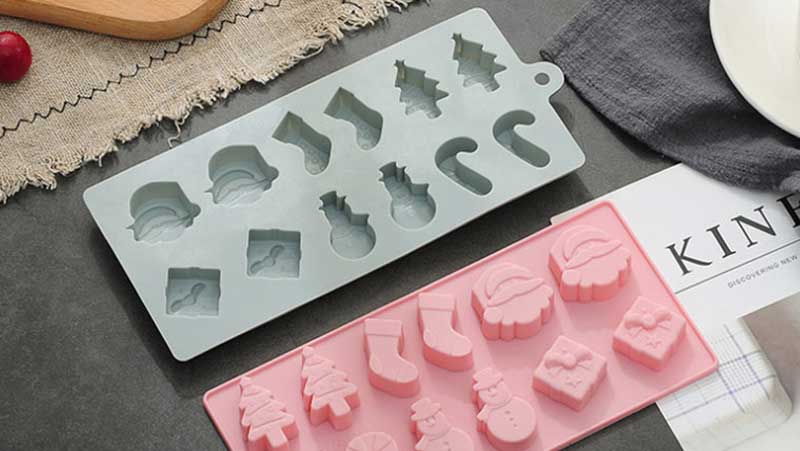
Advantages of Silicone Compression Molding
Silicone compression molding offers several advantages over other molding techniques:
1. Lower Tooling Costs – Compared to injection molding, compression molds are less expensive to manufacture, making this process ideal for low to medium production volumes.
2.Ideal for Large and Thick-Walled Parts – Since material is directly placed into the mold, there are fewer limitations on part size or weight.
3. Minimized Material Waste – Compression molding produces less scrap compared to high-pressure molding techniques, making it more cost-effective when working with expensive silicone formulations.
4. Flexible Production Runs – This method is suitable for both prototyping and batch production, allowing manufacturers to refine designs before committing to high-volume production.
5. Durability and High-Performance Properties – Silicone parts produced through compression molding exhibit high temperature resistance, excellent elasticity, and superior mechanical properties, making them ideal for demanding applications.
Limitations of Silicone Compression Molding
Despite its advantages, silicone compression molding has some limitations:
1. Slower Production Cycle – Compared to injection molding, compression molding has longer cycle times due to the manual material placement and curing process.
2.Not Suitable for Highly Complex Geometries – Parts with undercuts, intricate details, or extreme angles may require secondary processing or alternative molding techniques.
3. Flash Removal Increases Labor Costs – Excess material may form around the edges of the molded part, requiring manual trimming or deflashing.
4. Limited Precision in Dimensional Tolerances – While compression molding can achieve acceptable tolerances for most applications, it is not as precise as injection molding or CNC machining.
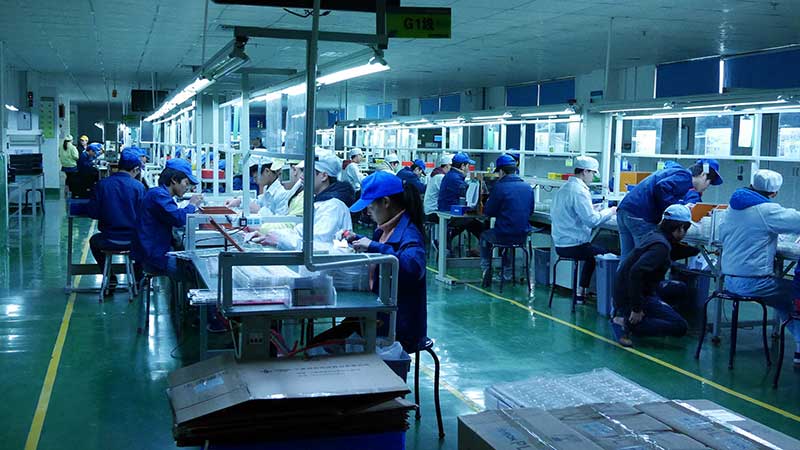
Applications of Silicone Compression Molding
Silicone compression molding is widely used in industries that require high-performance, hittebestendig, and durable silicone components.
1. Auto -industrie
- Afdichtingen en pakkingen – Prevent fluid leaks and contamination in engines and transmissions.
- Hoses and tubing – Withstand high temperatures and harsh conditions.
- Vibration dampening components – Reduce noise and mechanical stress in vehicles.
2. Medical Industry
- Silicone tubing and implants – Biocompatible materials for surgical applications.
- Protective covers and seals – Used in medical devices and diagnostic equipment.
3. Consumer Goods
- Kitchenware – Heat-resistant molds for baking mats, spatulas, and oven mitts.
- Protective cases – Silicone phone covers, electronic enclosures.
4. Electronics and Electrical Components
- Insulating gaskets – Used in electrical enclosures to prevent moisture damage.
- Connector seals – Ensure secure and weather-resistant connections.
Choosing the Right Silicone Molding Process
Manufacturers should consider several factors when choosing between compression molding and other molding methods:
- Batch Size – Compression molding is best for low to medium production volumes.
- Part Complexity – If parts require fine details or complex geometries, injection molding may be a better option.
- Cost Considerations – For cost-sensitive projects, compression molding offers lower upfront tooling costs.
Proper material selection, mold design, and quality control are essential to achieving optimal results in silicone compression molding.
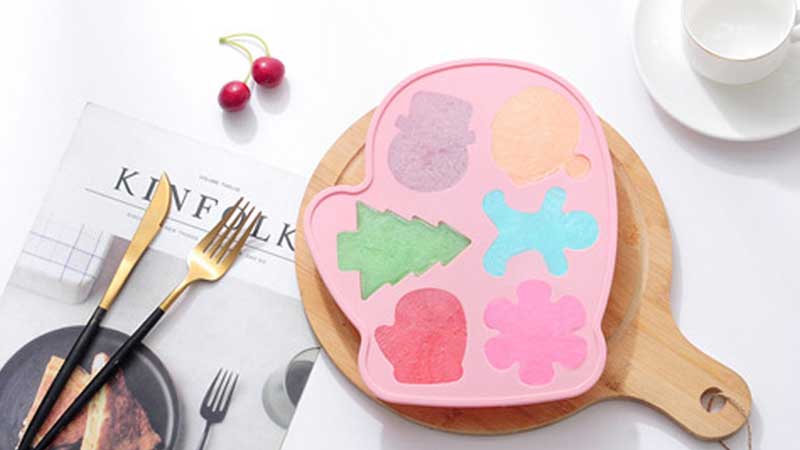
Conclusie
Silicone compression molding remains a reliable and efficient method for producing high-quality silicone components. Its ability to manufacture large, durable, and cost-effective parts makes it a popular choice in multiple industries.
While cycle times and precision tolerances may pose limitations, manufacturers can maximize efficiency by selecting the right mold materials, optimizing curing conditions, and implementing effective post-processing techniques.
For companies seeking a scalable, cost-efficient way to produce durable silicone parts, silicone compression molding remains an industry-leading solution.