실리콘은 많은 산업에서 사용되는 다재다능한 재료입니다., 내구성에 가치가 있습니다, 유연성, 극한 조건에 대한 저항. 다른 제조 공정은 실리콘을 다양한 제품으로 형성합니다, 각각 특정 용도 및 성능 요구를 위해 설계되었습니다. 주요 방법에는 다음이 포함됩니다 액체 실리콘 고무에 대한 사출 성형 (LSR) 그리고 일관성 고무 고무 (HCR), 압출, 캘린더링, 압축 성형, 전달 성형. 이러한 각 기술은 정밀도 측면에서 독특한 이점을 제공합니다., 생산 속도, 그리고 재료 효율성. 이러한 프로세스를 이해하면 품질을 최적화하는 데 도움이됩니다, 능률, 실리콘 제품 제조의 비용 효율성.

액체 실리콘고무 (LSR) 사출 성형
액체 실리콘고무 (LSR) 2액형이다, 고정밀 응용 프로그램을 위해 설계된 백금 경련 재료. 흐름이 가능합니다, 극한 온도에 매우 저항력이 있습니다, 자동화 된 생산에 적합합니다.
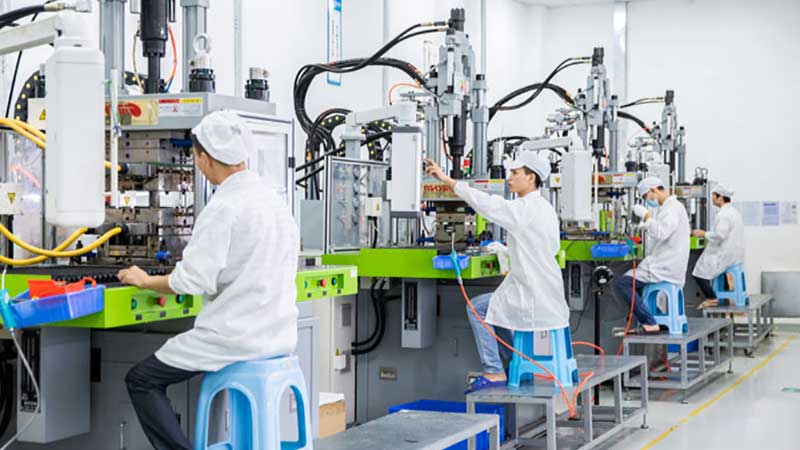
LSR 주입 성형 공정
LSR 주입 성형 공정은 투여 장치의 두 개의 액체 실리콘 성분 (촉매 및 교차 선수)의 혼합으로 시작됩니다.. 이러한 구성 요소는 정적 또는 동적 믹서로 공급되어 주입 장치로 펌핑되기 전에 동질성을 보장합니다.. 그런 다음 혼합 실리콘을 제어 압력 하에서 노즐을 통해 예열 금형에 주입합니다.. 곰팡이 안으로 일단, 재료는 빠르게 치료됩니다, 원하는 모양으로 굳어집니다.
LSR 주입 성형의 장점
- 짧고 정확한 성형주기, 효율성 향상.
- 대량 생산 능력, 대량 제조에 비용 효율적입니다.
- 최소 재료 폐기물, 더 나은 자원 활용을 보장합니다.
- 우수한 금형 방출 특성, 후 처리 노력 감소.
- 일관된 품질과 높은 정밀도, 의료에 이상적입니다, 자동차, 전자 응용 프로그램.
높은 일관성 고무 (HCR) 사출 성형
높은 일관성 고무 (HCR), 열 경화 고무 또는 고온 저온으로도 알려져 있습니다. (HTV) 실리콘, 더 두껍습니다, LSR에 비해 반죽 같은 일관성. 그것은 기계적 강도와 적응성으로 가치가 있습니다.
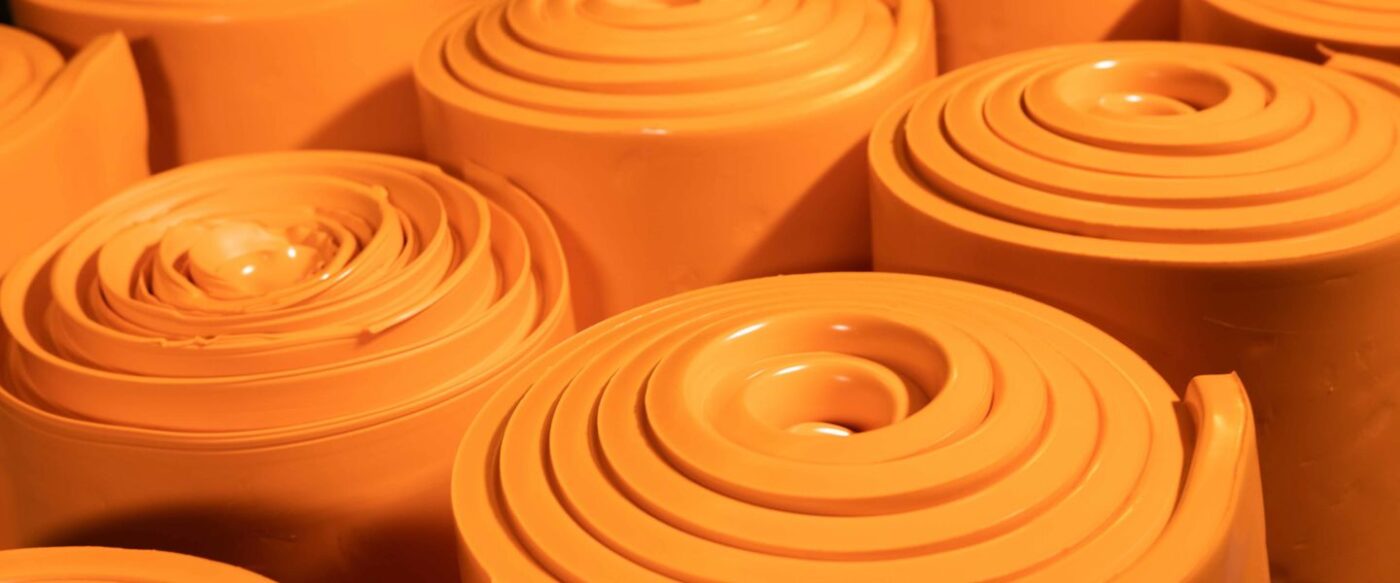
HCR 주입 성형 공정
HCR 주입 성형 공정은 원시 실리콘으로 시작합니다, 강도를 향상시키기 위해 FUMED 실리카와 같은 강화제와 혼합됩니다.. 그런 다음 화합물을 스트립으로 미리 형성하고 나사 압출기에 공급합니다., 집중 혼합 및 전단력을 겪고 균일하게 만드는 곳. 그런 다음 재료는 고압 노즐을 통해 가열 금형 공동으로 운반됩니다.. 가황은 높은 온도에서 발생합니다, 실리콘을 곰팡이 모양으로 굳 힙니다.
HCR 주입 성형의 장점
- 단위 비용 절감 효율적인 재료 사용으로 인해.
- 압축 성형에 비해 폐기물 감소.
- 혼합 재료 성형의 능력, 실리콘과 플라스틱 또는 금속을 결합합니다.
- 우수한 정밀 및 치수 안정성, 복잡한 부분의 경우에도.
- 다양한 응용 프로그램에 적응할 수 있습니다, 항공우주를 포함한, 보건 의료, 자동차 산업.
실리콘 고무 압출
실리콘 고무 압출은 주로 튜브와 같은 연속 프로파일을 만드는 데 사용됩니다., 개스킷, 물개, 그리고 단열재. 이 방법은 장장 제품의 균일 한 단면을 보장합니다.
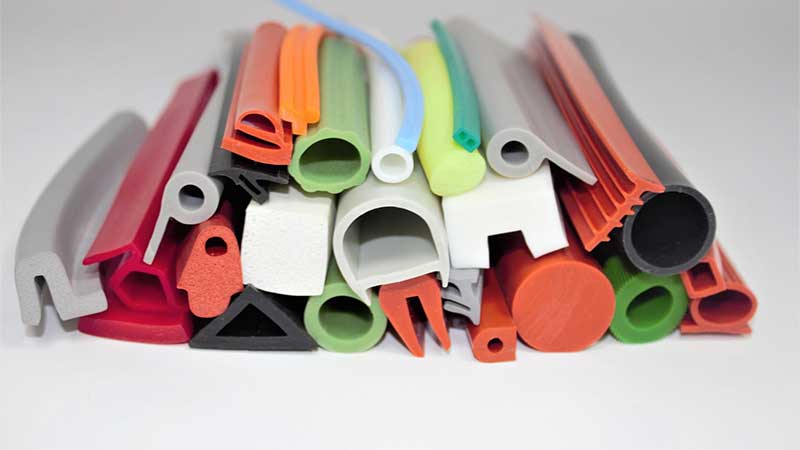
실리콘 압출 공정
압출은 원시 HCR 실리콘으로 시작합니다, 경화제로 공식화되고 스트립 또는 덩어리로 형성됩니다.. 이 사전 양식은 압출기에 공급됩니다, 회전하는 나사 메커니즘이 원하는 단면 모양으로 경화 된 강철을 통해 실리콘을 밀어 넣는 곳. 압출 프로파일은 고온 경화 오븐을 통해 지속적으로 당겨져 완전한 vulcanization을 보장합니다.. 이 과정의 일부 변형에는 공동 추출이 포함됩니다, 단일 패스로 여러 층의 실리콘 또는 추가 재료가 결합되는 경우.
실리콘 압출의 장점
- 일관된 출력, 유니폼 제품.
- 고속 생산, 대량 제조에 효율적입니다.
- 재료 제형의 다양성, 다층 디자인을 허용합니다.
- 유연성에 이상적입니다, 내열성, 내구성있는 구성 요소, 의료 튜브 및 자동차 씰과 같은.
실리콘 고무 캘린더
캘린더링은 정확한 두께와 표면 마감으로 연속적인 실리콘 고무를 생산하는 데 사용되는 특수 기술입니다.. 실리콘 코팅 된 직물 및 산업용 라이너를 생산하는 데 널리 사용됩니다..

실리콘 캘린더링 공정
이 과정은 원시 HCR 실리콘으로 시작합니다, 일련의 대형으로 공급되기 전에 가열되고 연화됩니다., 캘린더로 알려진 회전 스틸 롤러. 이 롤러는 실리콘을 얇게 압축하고 늘립니다, 균일 한 시트, 그런 다음 직물이나 기타 재료로 강화 될 수 있습니다.. 캘린더 실리콘 시트는 제어 된 난방 환경에서 치료되기 전에 양각 또는 질감을 가질 수 있습니다..
실리콘 캘린더링의 장점
- 마디 없는, 대량 생산, 대규모 응용 프로그램의 비용 절감.
- 맞춤형 텍스처 및 표면 마감, 기능 향상.
- 강화 재료를 통합하는 능력, 기계적 특성 향상.
- 산업용 컨베이어 벨트에 이상적입니다, 의료 등급의 영화, 보호 라이너.
실리콘 고무 압축 성형
압축 성형은 가장 오래되고 가장 비용 효율적인 실리콘 형성 방법 중 하나입니다., 단순하고 큰 부품을 생산하는 데 사용됩니다.

실리콘 압축 성형 공정
이 방법은 사전 측정 된 원시 실리콘으로 시작합니다, 예열 된 금형 공동에 수동으로 배치됩니다. 그런 다음 몰드는 고압하에 닫힙니다, 실리콘이 공동 전체에 균등하게 퍼지도록 강요합니다. 재료가 치료 될 때까지 열과 압력이 유지됩니다. 치료 후, 금형이 열린다, 그리고 트리밍 및 마무리를 위해 부품이 제거됩니다.
실리콘 압축 성형의 장점
- 툴링 비용 절감, 중소형 생산에 경제적으로 만듭니다.
- 최소 재료 폐기물, 비용 효율성 향상.
- 크거나 불규칙한 모양의 부품에 적합합니다, 사출 성형을 사용하여 생산하기가 어렵습니다.
- 두꺼운 벽을 생산하는 데 탁월합니다, 내구성있는 구성 요소, 자동차 씰 및 키패드와 같은.
실리콘 고무 전달 성형
전송 성형은 압축과 사출 성형의 측면을 결합합니다., 더 높은 정밀도와 효율성을 제공합니다.
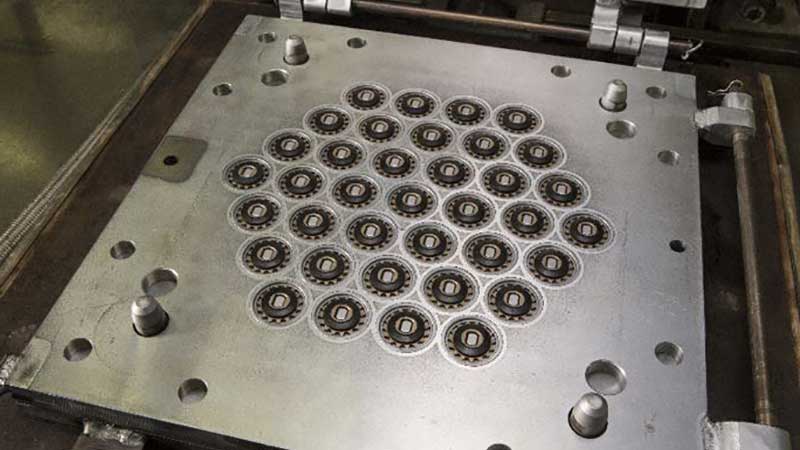
실리콘 전달 성형 공정
전송 성형에서, 사전 측정 된 HCR 실리콘은 폐쇄 된 금형 공동 위의 챔버에 배치됩니다.. 그런 다음 플런저는 채널을 통해 재료를 고압 하에서 가열 금형으로 강제합니다.. 이것은 더 나은 흐름 제어를 허용합니다, 금형 내의 재료의 분포를 보장합니다. 재료는 가황을 겪습니다, 그리고 치료 후, 완성 된 부분이 제거됩니다.
실리콘 전달 성형의 장점
- 사출 성형에 비해 툴링 비용이 낮습니다.
- 압축 성형보다 높은 정밀도 및 일관성.
- 강화 또는 다중 물질 부품을 생산할 수 있습니다.
- 오버 모딩 애플리케이션에 적합합니다, 실리콘을 다른 재료와 결합합니다.
결론
실리콘 제조 공정은 최종 제품의 요구 사항에 따라 다릅니다., 모양을 포함하여, 기계적 특성, 생산량. 사출 성형, 압출, 캘린더링, 압축 성형, 전달 성형 각각은 고유 한 혜택을 제공합니다, 실리콘 만들기 의료와 같은 산업에 적응할 수있는 자료, 자동차, 전자 제품, 그리고 소비재. 이러한 프로세스를 이해하면 제조업체는 특정 응용 프로그램에 가장 효율적이고 비용 효율적인 방법을 선택할 수 있습니다., 고품질 및 안정적인 실리콘 제품 보장.