Silicone Extrusion Manufacturer
Leading supplier of parts created by the silicone extrusion technology is LGDSilicone Parts. We are the perfect partner for your upcoming project thanks to our cutting-edge production capabilities, exceptional quality, and twenty years of experience with silicone rubber parts.
What Is Silicone Rubber Extrusion?
Silicone extrusions typically show a huge improvement over other materials – they last longer, come in a multitude of colours, and stand up to a wider variety of environmental conditions.
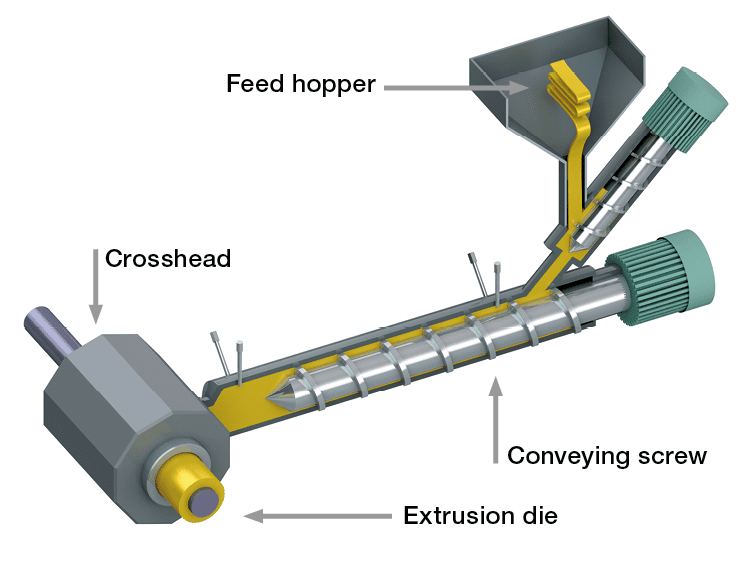
Proses Penyemperitan Silikon
Rubber extruding is a part forming process generally performed by rubber fabricators
- 1.Sebatian silikon dimasukkan ke dalam penyemperit
- 2.Langkah seterusnya melibatkan pemberian bahan dalam corong suapan
- 3.Bahan itu kemudian dimasukkan ke dalam seruling berbeza yang terdapat dalam skru pusingan
- 4.Skru akan mula membawa getah ke dalam dadu ke hadapan dan tekanan apabila bahan semakin hampir dengan dadu
- 5.Silikon kemudiannya dipaksa melalui die penyemperitan untuk membentuk profil yang diperlukan
- 6.Akhirnya,profil tersemperit melalui ketuhar yang menyembuhkan produk dengan haba sinaran
Industries and Applications
LDGSilicone supplies a wide range of custom Silicone Rubber molding parts. These parts can be found in products used in a wide array of industries, including automotive, Aerospace,Cookware, life sciences (such as medical/healthcare /baby care products), and Toy and special applications.
Custom Silicone Extrusion FAQs
Extruded silicone is relatively clear, which makes it easy to color in applications with specific organizational or aesthetic needs. It also makes it well-suited for the fabrication of clear tubing. Resistant to high temperatures. Most common silicone extrusions can handle temperatures as high as 500°F.
Silicone has some unique properties that make it preferable to other materials in some specific circumstances.
These include:
>Excellent temperature resistances,with standard ranges from -60C to +200C and higher temperature grades available if required.
>Flexibility and integrity,helping to keep its shape and maintain a perfect seal Resistance to oil,bahan kimia,heat and water
>Available in any color you require
The large range of liquids and pastes that can be processed makes extrusion-based technologies a clear advantage. Thus, practically all silicones can be used: From low to high viscosity, standard LSR to UV-curing and particle-filled silicones, as well as RTV (room temperature vulcanization).
EXTRUSION After that, the silicone compounds proceed through the extrusion process, when the tool (die) actually carves the contour. Following a heating phase without external pressure (pressureless vulcanization), addition curing with a platinum catalyst or peroxide curing are used.
Extruded silicone is relatively clear, which makes it easy to color in applications with specific organizational or aesthetic needs. It also makes it well-suited for the fabrication of clear tubing. Resistant to high temperatures.
Silicone Rubber Molding Other Production Capabilities
LGDSilicone offers several options for Silicone Rubber Molding Production Capabilities
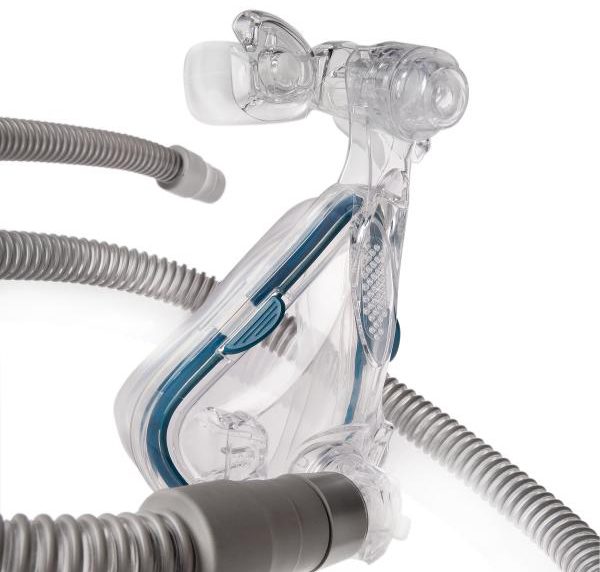
Silicone Overmolding
Silicone over-molding involves placing a metal or plastic part into a mold cavity and heating it to cure it

Compression Molding
Silicone Rubber Compressing Molding is the process of Compression Molding with Silicone Rubber as the material.
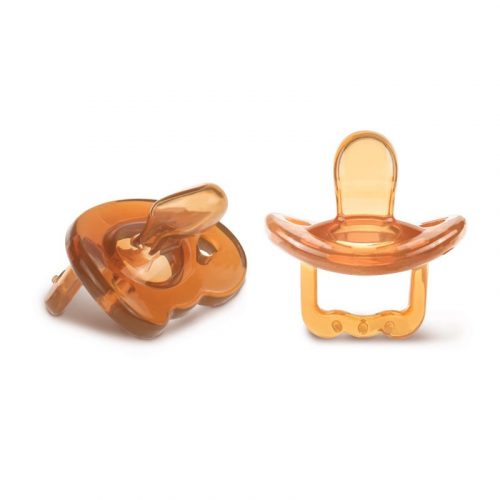
Pengacuan Suntikan LSR
LSR Injection Molding is the process of injecting Liquid Silicone Rubber into the molding machine to make the part.

Kalender Silikon
Silicone calendering is a mechanical process used to manufacture uniform sheets made of silicone rubber