Injection molding is supported by both liquid silicone rubber (LSR) and high consistency rubber (HCR).
The primary differentiator between liquid rubber and high-consistency rubber is the “flow” or “liquid” nature of LSR materials. LSR has an addition/cure/platinum cure whereas HCR has a peroxide cure. LSR is made up of a liquid silicone rubber substance with a very low viscosity that may be cast or injected into rubber sheets.
Despite having comparable physical characteristics, they need radically distinct processing methods. Designers may choose the optimum production process for their silicone components and products by knowing how LSR and HCR injection molding functions.

What is LSR Injection Molding?
A base material and a catalyst, a vulcanizing chemical that transforms liquid silicone rubber into a solid substance, are used in LSR injection molding. The majority of LSRs employ an addition reaction-based curing mechanism based on platinum. Although curing may be accelerated by applying heat or pressure, LSRs cure more rapidly than HCRs. Imidlertid, LSR injection molding offers even more benefits.
Meter-mixing is the first step of LSR injection molding. The ingredients are dispensed via a pump, and they are combined by a static mixer. Derefter, a cooled portion of the injection molding machine receives this mixture. LSRs promote consistency within and between individual pieces since the material is homogenous. For increased productivity, LSR injection molding also allows automated processes.
Application of LSR Injection Molding
LSR often finds application in products that require a high level of precision, herunder følgende:
- Seals/Gaskets
- portable communications cushioning
- pacifiers and bottle nipples for babies
- wiring connectors
- Medicinal purposes (actuators, septum, dosing valves)
- Wearables for medicine delivery and health monitoring
Liquid Silicone Rubber has also developed into a popular material for over-molding onto other components made from a range of polymers.
When Is Liquid Silicone Rubber (lsr) The Best Choice?
Because it enables producers to generate multiple duplicates of a material through an automated reduplicated process, flydende silikonegummi (LSR) is an extremely versatile and accurate injection molding technique.
When low manufacturing costs are necessary, flydende silikonegummi (LSR) injection molding is the best and most popular option. Because it enables mass production in a shorter amount of time and yields more exact materials, flydende silikonegummi (LSR) injection is most chosen by the medical industry when it comes to cost effectiveness. Non-sealed equipment manufacturing sectors also utilize this technology more frequently.
Since the liquid silicone rubber (LSR) process is constantly automated, flydende silikonegummi (LSR) is the ideal option when labor is scarce.
What is HCR Injection Molding?
Solid silicone rubber (sometimes referred to as high-consistency silicone rubber, or HCR), which is cured at high temperatures using either organic peroxides or a platinum catalyst. HCR has a firm consistency because it comprises long polymer chains with a high molecular weight. HCR is employed in a variety of static and dynamic applications due to its exceptional mechanical qualities, inklusive:
- Automotive
- Rumfart
- Electrical transmission and distribution
- Wire and cable
- Fødevareforarbejdning
- Molded rubber goods
Excellent aging and temperature resistance is provided by HCR. Conventional techniques including extrusion, calendering, compression, and injection molding can be used to process it.
The HCR Injection Molding Process
The actual silicone rubber manufacturing process five steps:
- Catalysation and Mill Softening
This initial process reverses any "crepe hardening" that occurs as a result of the material being stored at the supplier or fabricator and is necessary for both extrusion and molding applications.
- Constructing a Preform
A plug that fits in the transfer reservoir of the transfer press must be cut from the preform by a die-cutter as part of the transfer molding procedure.
- Ekstrudering
A single-screw extruder is used in the extrusion press for HCR. A roller feed wheel is used by the operator to feed prefabricated strips into an extruder.
- Molding
Different molding tools are needed for various high-consistency silicone applications.
- Vulcanization
The extruded profile is pulled up through the oven in the vertical oven, which is available in both vertical and horizontal variants.
When Is High Consistency Rubber (HCR) The Best Choice?
High Consistency Rubber (HCR) injection molding is frequently the preferred method when producing equipment and materials parts for the automotive, electrical, biomedicinsk, and pharmaceutical industries. High Consistency Rubber (HCR) exhibits high resistance to temperature, is an excellent shock absorber, and is a good electricity conductor.
High Consistency Rubber (HCR) is the finest option for the fabrication of cables, spark plug boots, electrical insulators, tubes, aviation equipment, and other sealed equipment because to its strong heat resistance, fire resistance, and low smoke discharge.
Because the procedure isn't adaptable enough for automated replication needed for mass production runs, the High Consistency Rubber (HCR) molding method is the best option in cases of big manufacturing.
LSR sprøjtestøbning vs HCR sprøjtestøbning
When the following factors are properly considered, it is easy to decide which molding technique is best for your project. Both molding processes have their own unique benefits.
1.Production volume
The size of production you hope to attain should be a definite deciding element when selecting the sort of injection molding technique to utilize. Flydende silikonegummi (LSR) injection molding is the most appropriate for large-scale manufacturing whereas High Consistency Rubber (HCR) injection molding is not.2.
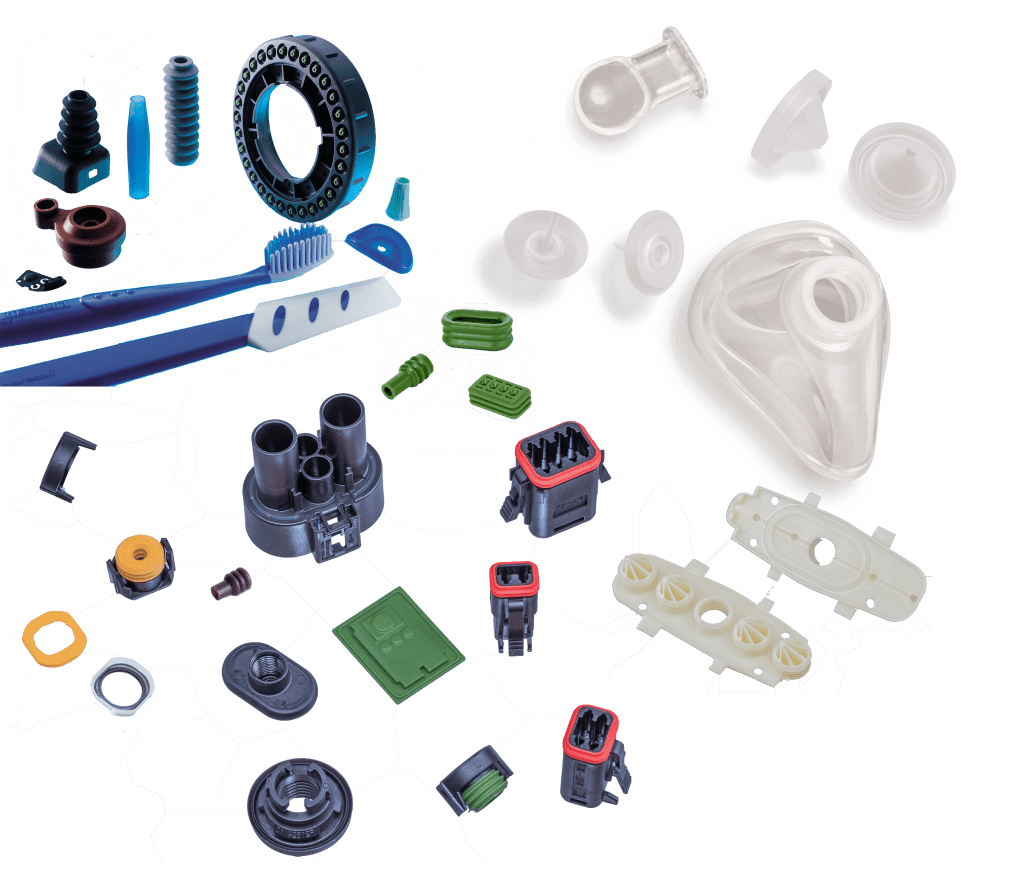
2. Massefylde
The required degree of hardness of the final product also influences the molding technique to be used. The density of liquid silicone rubber (LSR), which ranges from 10 durability to 70 holdbarhed, is above (10 durometer - 80 durometer Shore A). Compared to high consistency rubber, flydende silikonegummi (LSR) creates materials that are softer and more flexible (HCR).
3. Production costs
In terms of cost effectiveness, Flydende silikonegummi (LSR) is recommended over High Consistency Rubber (HCR). Unlike high consistency rubber (HCR) sprøjtestøbning, flydende silikonegummi (LSR) requires less labor and is simpler to create.
4. Resilience
This is a gauge of a material's resistance to wear, pressure, and damage. Divide the material's length by its elastic limit to determine how durable it is. A solid silicone has a typical durability of 9.8 kN/m. Compared to high consistency rubber, flydende silikonegummi (LSR) generates more durable products (HCR).
The ultimate selection about the production method for either liquid silicone rubber (LSR) or high consistency rubber (HCR) depends on the preferences of the producer and the parameters necessary for the material.
How do the two compare?
LSR is simpler to produce and is more suited for usage on complicated geometries. Greater overall properties are possible with HCR. While LSR provides a wider range of material options.
The great majority of its consumers prefer LSR. Generally speaking, the expenses of HCR are greater than those of LSR.
Mold Types of LSR and HCR

Which One is Right for You?
Many of the performance benefits shared by HCR and LSR apply to both. The quantity of pieces your project requires will ultimately determine the best material to use. Generelt, LSR materials work well for high-volume manufacturing or tight tolerances since it keeps unit prices low, whereas HCR materials are better suited to smaller production runs. As demand increases, the initial manufacturing will move to either HCR or LSR.
Our specialists can provide a recommendation if you need assistance choosing the appropriate material for your application. Wacker silicone elastomers are available in a wide range from us to satisfy your specific needs.