High Consistency Rubber (HCR) or Heat Cured Rubber (HCR) is an injection molding technique used to create equipment with high consistency polymeric silicone that is resilient and elastic.
The Strong Consistency Rubber (HCR) is a flow plate with a high resistance to flow and little elasticization. High Consistency Rubber (HCR) is suitable for tough environmental circumstances because it has excellent shock absorption, heat and cold resistance, and electrical conductivity.
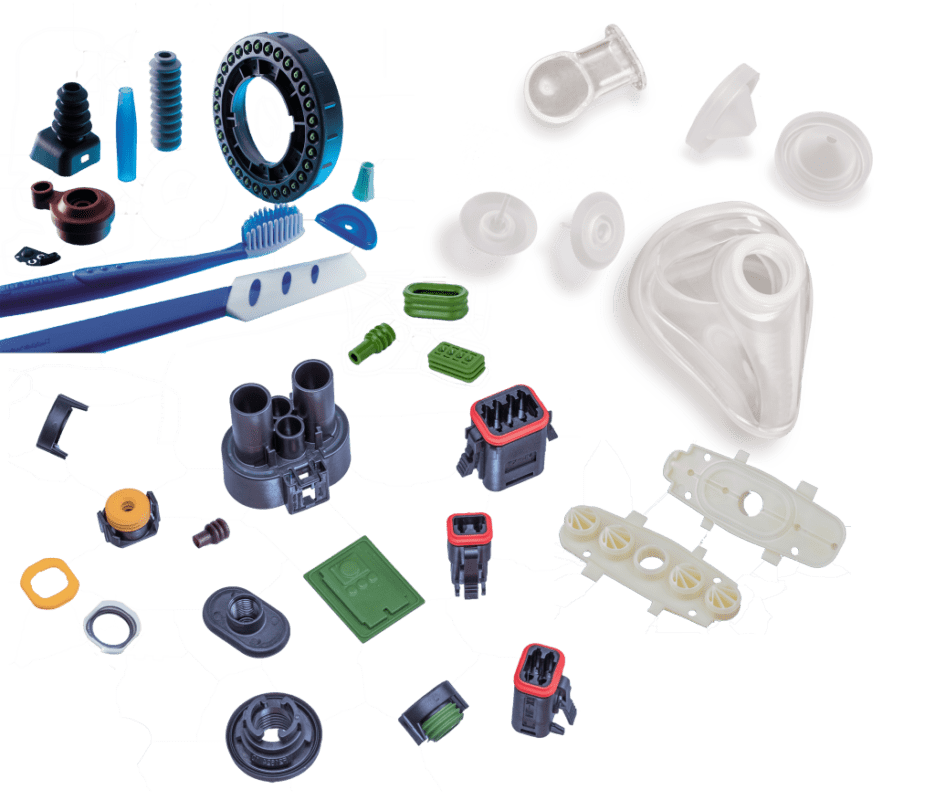
What is High Consistency Rubber(HCR)?
Solid silicone rubber (sometimes referred to as high-consistency silicone rubber, or HCR), which is cured at high temperatures using either organic peroxides or a platinum catalyst. HCR has a firm consistency because it comprises long polymer chains with a high molecular weight. HCR is employed in a variety of static and dynamic applications due to its exceptional mechanical qualities, inklusive:
- Automotive
- Rumfart
- Electrical transmission and distribution
- Wire and cable
- Fødevareforarbejdning
- Molded rubber goods
Excellent aging and temperature resistance is provided by HCR. Conventional techniques including extrusion, calendering, compression, and injection molding can be used to process it.
The HCR Injection Molding Process​
Solid silicone rubber is produced in bulk by rubber producers, who combine the ingredients in an uniform mixture at high temperatures. The curing process is facilitated by the inclusion of peroxide catalyst. Fabricators start the cross-linking of the molecules, but roll out the sheets of rubber materials before the vulcanization process is finished for storage or transportation.
The actual silicone rubber manufacturing process entails six steps:
- Catalysation and Mill Softening
This initial process reverses any "crepe hardening" that occurs as a result of the material being stored at the supplier or fabricator and is necessary for both extrusion and molding applications. Derudover, some procedures employ milling to combine the two components of an extra cure elastomer before processing or to add peroxide catalysts as needed to a free radical elastomer. A two-roll mill is required for this time-consuming procedure since the elastomer must go through the mill more than once to combine the complex material into a homogenous final result. The sheet might need to be processed further once it has been taken out of the mold.
- Constructing a Preform
The preparation of a performance comes next, which entails a lot of work, especially in high-volume production settings that run continuously. A plug that fits in the transfer reservoir of the transfer press must be cut from the preform by a die-cutter as part of the transfer molding procedure. Due to the requirement that the preform be cut into the same shape as the finished component, the compression molding application involves a more involved procedure. The elastomer sheet is cut into strips and fed into the extruder to prepare the preform for the extrusion and injection molding applications.
- Ekstrudering
A single-screw extruder is used in the extrusion press for HCR. A roller feed wheel is used by the operator to feed prefabricated strips into an extruder. The elastomer material is extruded through a die and mandrel assembly, which equips the extruder with a crosshead assembly to form the required profile. Det "support extrude" processing option uses a crosshead assembly that is mounted on the extruder to pass the supporting geometry through it and extrude a layer of silicone rubber over it.
- Molding
Different molding tools are needed for various high-consistency silicone applications. Personnel are needed to load the elastomer into the machinery and to de-mold the completed components during both transfer and injection molding manufacture. In order to complete the compression molding process, employees must insert preforms into each mold's cavity. Due to the long cure cycles of high consistency rubber, the molds may have several holes.
- Vulcanization
Extruded goods are vulcanized by fabricators using hot-air vulcanizing ovens (HAVs). By creating molecular cross-links, this process makes the material stronger and more resilient. The extruded profile is pulled up through the oven in the vertical oven, which is available in both vertical and horizontal variants. Radiant heat or a steam autoclave oven are used in some vulcanization procedures.
- Finishing
The application determines how much finishing is done. The finishing procedure for extrusion profiles involves a visual examination and cutting the tubes into predetermined lengths. The profile has to go through a post-cured procedure to get rid of the peroxide byproducts for extrusion components that are peroxide cured. Trimming or de-flashing of molded components is another step in the injection molding process. The employee cuts the components off the huge, molded sheet using a die-cutting tool. The component can need post-curing in specific circumstances.
Material is wasted during the production of high-consistency rubber, and labor is expensive. Derudover, physical labor and other tools and equipment are needed. Imidlertid, the equipment is less costly than the molds needed to make items made of LSR (flydende silikonegummi).
When Is High Consistency Rubber (HCR) The Best Choice?
High Consistency Rubber (HCR) injection molding is frequently the preferred method when producing equipment and materials parts for the automotive, electrical, biomedicinsk, and pharmaceutical industries. High Consistency Rubber (HCR) exhibits high resistance to temperature, is an excellent shock absorber, and is a good electricity conductor.
High Consistency Rubber (HCR) is the finest option for the fabrication of cables, spark plug boots, electrical insulators, tubes, aviation equipment, and other sealed equipment because to its strong heat resistance, fire resistance, and low smoke discharge.
Because the procedure isn't adaptable enough for automated replication needed for mass production runs, the High Consistency Rubber (HCR) molding method is the best option in cases of big manufacturing.