Wanneer u op zoek bent naar rubberafdichtingsartikelen voor uw project, it’s crucial to understand which material is appropriate for you. Today, we will look at fluorosilicone vs silicone, two kinds of rubber that have their own distinct qualities and various benefits.
Before you pick which material is appropriate for your project, it’s crucial to grasp the difference between these materials and which applications each is utilized for.
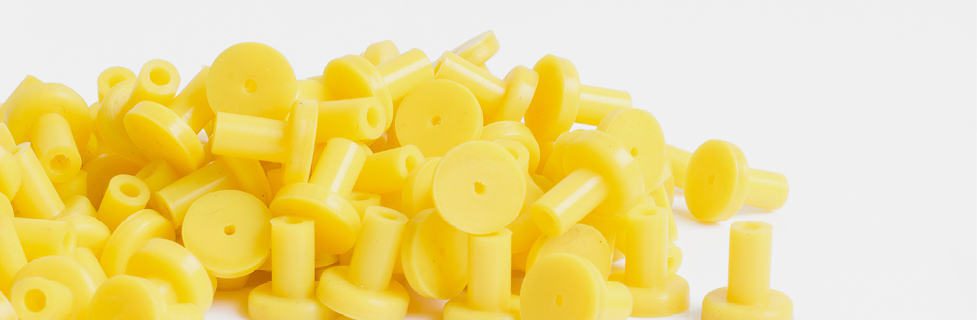
What is fluorosilicone?
Fluorosilicone rubber(FVMQ)is a variety of silicone rubber that maintains outstanding high-temperature stability and mechanical qualities while giving improved resistance to gasoline, oil, and other chemicals.
The unique features of fluoro silicone make it a problem-solving material widely utilized in industrial, aerospace, automobiel, and aviation applications for static sealing and cushioning.

The benefits of Fluorosilicone
- Broad working temperature (-70C to 200C); good low temperature performance compared to dimethyl LSR and FKM
- Offered in 30, 40, En 60 ShoreA, mechanical qualities equal to normal LSRs
- Lage compressie ingesteld
- High resistance to non-polar hydrocarbon fuels, oliën, and solvents;
- equivalent to normal high-consistency FSR grades
- Compatible with typical injection molding equipment
- Quick cycle times and low material waste
The Disadvantages of Fluorosilicone
Secondly, as indicated earlier, fluorosilicone is costly. This is because the synthesis of the fluorosilicone rubber monomer is highly complex and time-consuming, and the insertion of fluorine-containing groups enhances the difficulty of the vulcanization process, which pushes the manufacturing cost fairly high.
Second, fluorosilicone does not function well in settings that demand abrasion resistance.
Finally, while chemical resistance is a significant attribute of the fluorosilicone family of elastomers it does not do as well when resisting braking fluids, ketonen, hydrazine, amines, aldehyden, and ketones.
Applications for Fluorosilicone
Fluorosilicone’s particular resistance features make it the best choice for the aerospace sector, as well as oil and gas applications. Comparable to silicone, fluorosilicone is typically molded into o-rings, pakkingen, slangen, and other seals. Fluorosilicone is recommended for the following applications:
- Jet fuel systems
- Car gasoline emissions control systems
- Petroleum oil uses
- Chlorinated solvent environments
- Fuel cell gasketing
- Turbocharger hoses
- Intercooler hoses
Fluorosilicone O-rings, Gaskets Tubing, And Seals
Fluorosilicone’s particular qualities make it perfect for use in the sealing solutions found in engines, machinery, and other mechanical systems. Popular fluorosilicone sealing components include:
- O-rings. Shaped like a donut, O-rings are normally situated into a groove on one or both of the linked pieces where they create a seal, where that restrict the escape of air and fluids by filling up the space between related components.
- Pakkingen. Gaskets offer a flexible seal between two linked components. They are normally flat and relatively thin, having bolt or pin penetrations through them. Compressed between two flat surfaces, gaskets offer to seal as well as vibration control.
- Zeehonden. This is a broad word for any component that prevents fluid/air leaking fluids, inhibits pollutants, or maintains pressure. O-rings and gaskets are forms of seals, but the phrase generally pertains to application-specific sealing solutions kept in place by compression, such as oil seals used in engines.
- Slangen.
O-rings, pakkingen, and seals occupy the gap between two linked pieces of a machine or engine, allowing for the conveyance or transfer of fluids or air between them without leakage. Beyond fluid and vapor leaks, these components prevent debris from flowing into mechanical systems and maintain stable pressures to guarantee maximum operation.
Applications for Silicone
Silicone rubber finds applications in a variety of fields, including electrical insulation, automotive parts, and medical equipment
- in the food field. It can withstand high temperatures and its low toxicity makes it ideal for use in food-related applications. Its non-stick properties make it an excellent choice for cookware, bakeware, and other kitchen items.
- in the medical field, silicone is used in products such as catheters, slangen, and other devices that need to be resistant to temperature changes.
- In automotive parts, such as hoses, pakkingen, and seals, silicone rubber is valued for its excellent durability and vibration absorption.
- In the electrical industry, silicone insulators are preferred for their superior insulation capabilities.
What’s the difference between Fluorosilicone and Silicone?
Siliconen (VMQ) is formed of silicon, an element produced from quartz. This synthetic elastomer is made from pendant organic groups such as methyl, phenyl, and vinyl bonded to silicon atoms. Silicone has great heat and ozone, has high dielectric stability, and is resistant to various oils, Chemicaliën, and solvents. It is one of the finest elastomers for flexibility at low temperatures. It functions well in engine and transmission oil, diluted salt solutions, moderate temperature water, and dry heat.
Fluorosilicone (FVMQ) is a form of silicone rubber that remains stable at high temperatures and can survive harsh weather conditions including ozone. It also offers higher fuel and mineral oil resistance, but inferior hot air resistance than normal silicone. Fluorosilicone excels in fuels, aromatic mineral oils, benzene, toluene, and chlorinated and aromatic hydrocarbons.
Siliconen (VMQ) is formed of silicon, an element produced from quartz. This synthetic elastomer is made from pendant organic groups such as methyl, phenyl, and vinyl bonded to silicon atoms. Silicone has great heat and ozone, has high dielectric stability, and is resistant to various oils, Chemicaliën, and solvents. It is one of the finest elastomers for flexibility at low temperatures. It functions well in engine and transmission oil, diluted salt solutions, moderate temperature water, and dry heat. Fluorosilicone (FVMQ) is a form of silicone rubber that remains stable at high temperatures and can survive harsh weather conditions including ozone. It also offers higher fuel and mineral oil resistance, but inferior hot air resistance than normal silicone. Fluorosilicone excels in fuels, aromatic mineral oils, benzene, toluene, and chlorinated and aromatic hydrocarbons.
What are the different types of Fluorosilicone?
Fluorosilicone is available in both standard and custom formulations. Standard fluoro silicones include general-purpose fuel oil-resistant grades that are ideal for a variety of applications. Specialty fluoro silicones offer excellent performance in extreme temperatures, high pressures, and harsh chemical environments. The different types of fluoro silicone compounds include:
- Fluorosilicone rubber: This is the most common type of fluoro silicone used for industrial applications such as seals, pakkingen, O-rings, and others. It offers excellent resistance to oils, fuels, and chemicals.
- High-temperature fluorosilicone: This type of fluorosilicone has improved heat resistance and can withstand temperatures up to 330°C (626°F). It is commonly used in aerospace, automobiel, and electrical applications.
- Fuel-resistant fluoro silicone: This type of fluoro silicone offers excellent fuel resistance and is ideal for use in fuel systems or gasoline-powered engines.
- Low compression set fluorosilicone: This type of fluorosilicone has a low compression set and is used for valve stem seals, O-rings, and other applications that require dynamic sealing.
- Flame retardant fluorosilicone: This type of fluorosilicone offers good flame resistance and can be used in electrical insulation applications.
- Fluorosilicone elastomer: This type of fluorosilicone is used for gaskets, zeehonden, and other applications that require superior chemical resistance.
- High-performance fluorosilicone: This type of fluorosilicone offers superior physical properties and is used in harsh environments or where high temperatures are encountered.
- Low-temperature fluorosilicone: This type of fluorosilicone has improved low-temperature performance, allowing it to be used in cold temperatures. It is also resistant to ozone and weathering.
- Specialty fluorosilicones: These compounds offer unique properties such as high tensile strength, flame resistance, and low compression set. They are ideal for applications that require specialized performance.
Fluorosilicone vs Silicone For Material Properties

Fluorosilicone | Siliconen | |
Temperature resistance for Standard Compound | -60° C (-76°F) to 177°C (350°F) | -60° C (-76°F) to 225°C (437°F) |
Temperature resistance for Special Compound | -60° C (-76°F) to 232°C (450°F) | -100° C (-150°F) to 300°C (572°F) |
Hardheid | 40 naar 80 Shore A | 20 naar 80 Shore A |
ASTM D1418 Designation | FVMQ | Q, MQ, VMQ, PVMQ |
ASTM D2000 Designation | FK | FC, FE, GE |
Standard Color for shelf items | Blauw | Rust |
Fluorosilicone and Silicone FAQs
Is fluorosilicone the same as FKM?
Both materials are well-suited for use in temperatures ranging from -30°C to 180°C. Fluorosilicone has an advantage in lower temperatures, while FKM has an advantage in higher temperatures. When comparing these materials in terms of electrical current resistance, fluorosilicone has a slight advantage. The differences in compression set resistance show that FKM has a significant advantage.
In terms of wear resistance, FKM has a significant advantage. Echter, both materials have poor heat stability and fair short-term resilience. Fluorosilicone has a slight advantage in oil and gasoline resistance.
When choosing between these two materials, the primary decision should be based on the application’s temperature range, electrical current resistance needs, and wear characteristics. Depending on the requirements, either material could be suitable for use in an application. Aanvullend, both materials can offer outstanding performance when applied correctly.
Is Fluorosilicone expensive?
Fluorosilicone is an expensive material, primarily due to the difficulty and time-consuming nature of synthesizing the fluorosilicone rubber monomer. Aanvullend, the introduction of fluorine-containing groups increases the difficulty of the vulcanization process, which drives up production costs significantly.
What is the difference between silicone and Fluorosilicone?
Silicone is known for its excellent flexibility and elongation, while fluorosilicone has a higher resistance to heat and chemical degradation, as well as higher tensile strength and tear resistance. Each type of elastomer has specific uses depending on the required properties.
fluoroelastomer is a better choice for applications that require chemical resistance and high-temperature resistance, while silicone rubber is a better choice for applications that require heat resistance, weather ability, and electrical insulation properties.
Is Fluorosilicone rubber or plastic?
Fluorosilicone is an elastomeric material made of fluoroelastomers, combining the characteristics of fluorocarbon and silicone rubbers, not plastic. It is highly resistant to heat, aggressive chemicals, fuels, oliën, solvents, weathering, ozon, radiation, extreme temperatures, and water absorption. Fluorosilicone also exhibits excellent dielectric and flame-retardant properties.
Als gevolg, it finds use in a wide range of applications, including aerospace components and seals, automotive parts, wire insulation, electrical connectors, and gaskets. Fluorosilicone is particularly useful in automotive hoses and fuel lines due to its resistance to gasoline and diesel fuels. Overall, it is a versatile material that can be used across a variety of industries and applications.
Wat zijn de 4 types of silicone?
There are several types of silicone, each with unique properties that make them ideal for certain applications. Here are some of the most common types and their uses:
- Fluorosilicone: This type of silicone is often used when resistance to extreme temperatures, fuels, and lubricants is required. It also resists water absorption and maintains its properties over a wide temperature range.
- High-Temperature Silicone: Designed to withstand temperatures up to 500°F (260° C), this silicone retains its properties when exposed to temperatures as low as -60°F (-51° C). It is often used in automotive and aerospace applications.
- Platinum-Cured Silicone: This type of silicone is commonly used for medical purposes such as tubing and catheters because it is safe for use in contact with blood, body fluids, and tissues. It meets the biocompatibility requirements of USP Class VI and ISO 10993-1 standards.
- Vulkaniseren op kamertemperatuur (RTV) Siliconen: This type of silicone cures without the aid of heat or pressure, making it well-suited for applications where heat is an issue or there are limited space constraints. RTV Silicone can be used to create durable seals and adhesives that offer excellent UV resistance, high-temperature stability, and long-term durability.
What color is Fluorosilicone?
Fluorosilicone is usually available in black, wit, and red colors. Echter, it can be custom-colored to meet specific requirements.
Is Fluorosilicone conductive?
The conductive fluorosilicone elastomer has a 45-durometer and is electrically conductive. Regular fluorosilicone, aan de andere kant, is not conductive.
Conclusie
If you have an application that requires products made from fluorosilicone rubber, please contact our sales department at sale@lgdsilicone.com for further information.