Silicone Rubber Molding Manufacturer
LGDSilicone Parts is a leading provider of produced parts using the silicone rubber molding process. LGDSilicone offers comprehensive solutions for Silicone Rubber Molding applications realized
Silicone Molding Manufacturers Service
As a leader and pioneer in the industry, we know silicone rubber molding inside and out. we take a complete systems approach and advanced technology, automation and quality planning are the foundation.
At Lgdsilicone, Our engineers and technical team work together to determine the best solution that will meet our customers’ product objectives, add value, and that will measure-up to our own internal high standards for quality, efficiency, and productivity.
We offer a full portfolio of services, including: Design & Prototyping, Production and Value-Added Inline Operations.
Silicone Rubber Molding Other Production Capabilities
LGDSilicone offers several options for Silicone Rubber Molding Production Capabilities

Compression Molding
Silicone Rubber Compressing Molding is the process of Compression Molding with Silicone Rubber as the material.
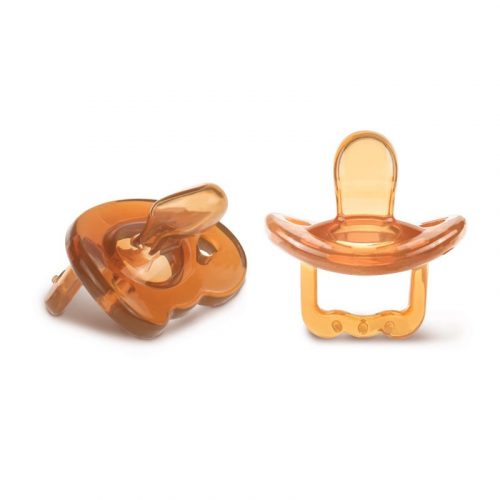
LSR Injection Molding
LSR Injection Molding is the process of injecting Liquid Silicone Rubber into the molding machine to make the part.
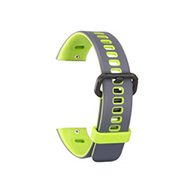
HCR Injection Molding
HCR silicone injection molding process typically involves heating the raw material and injecting it under high pressure into a mold.

Silicone Extrusion
Silicone extrusion is the process in which silicone is forced through a shaped die in to produce a continuous formed length
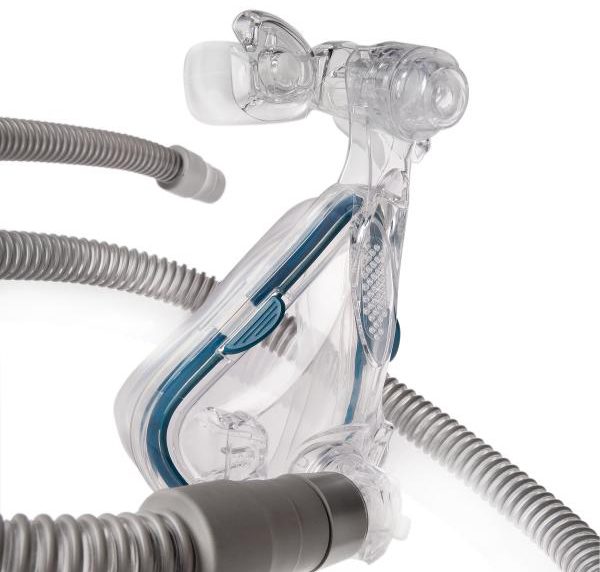
Silicone Overmolding
Silicone over-molding involves placing a metal or plastic part into a mold cavity and heating it to cure it

Silicone Calendering
Silicone calendering is a mechanical process used to manufacture uniform sheets made of silicone rubber
Mold Of Silicone Products
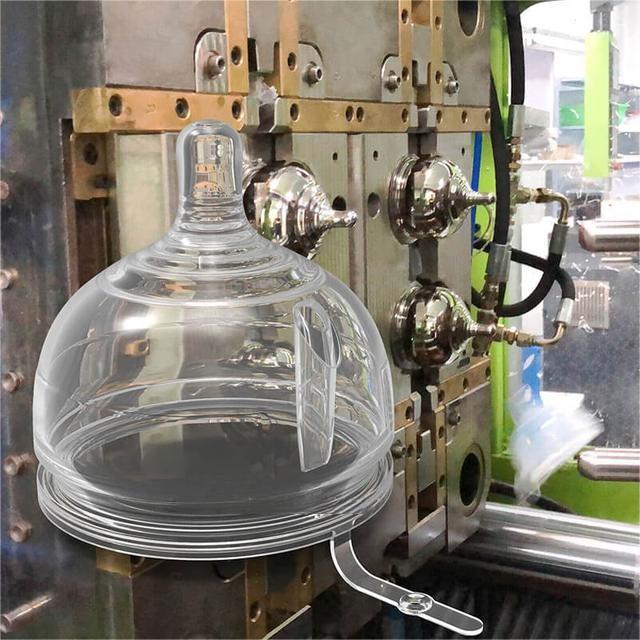
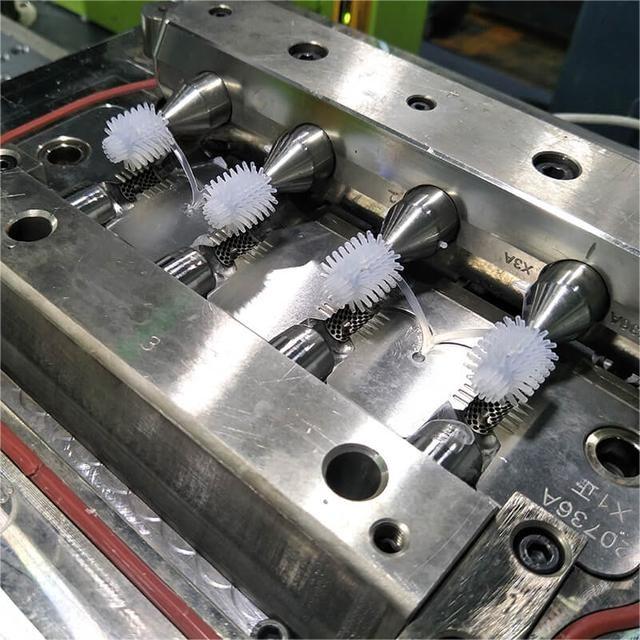
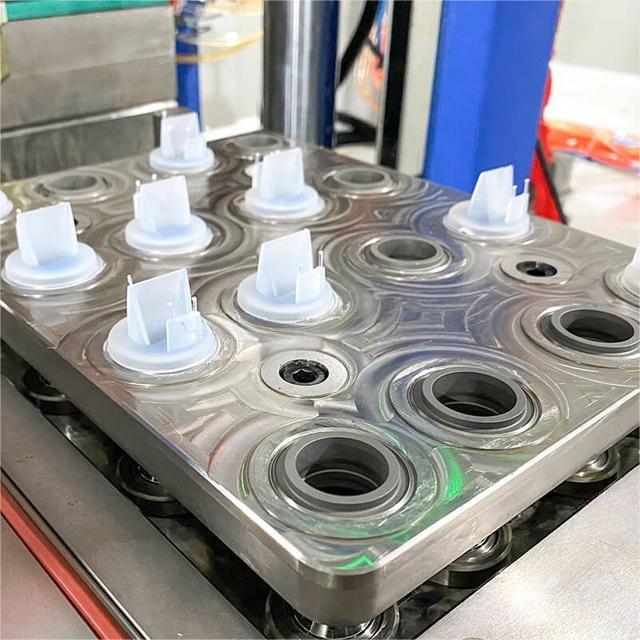
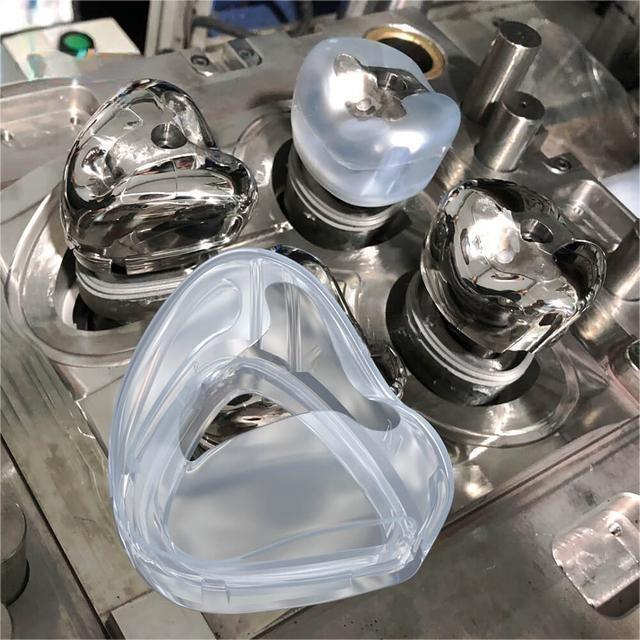
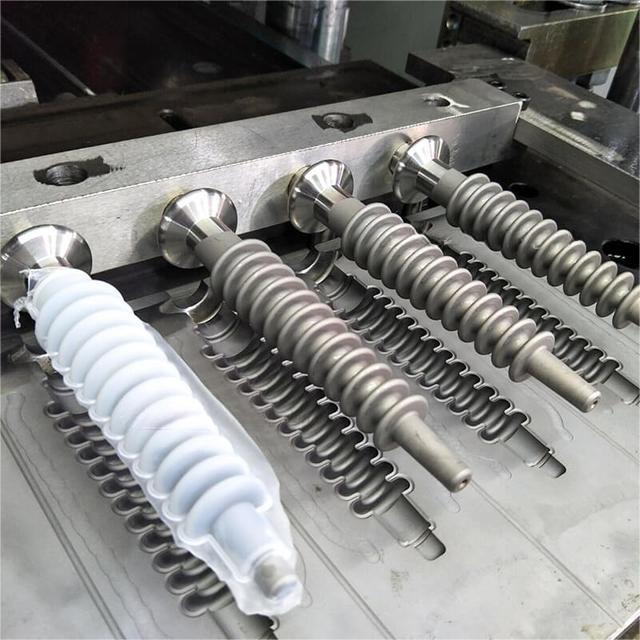
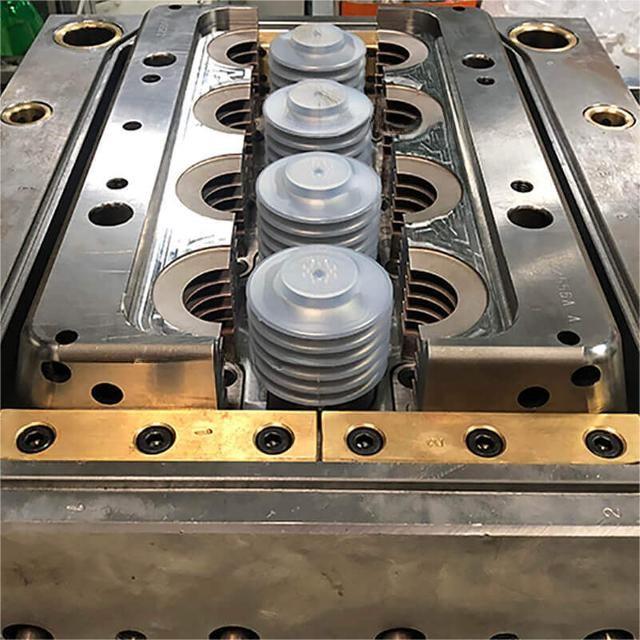
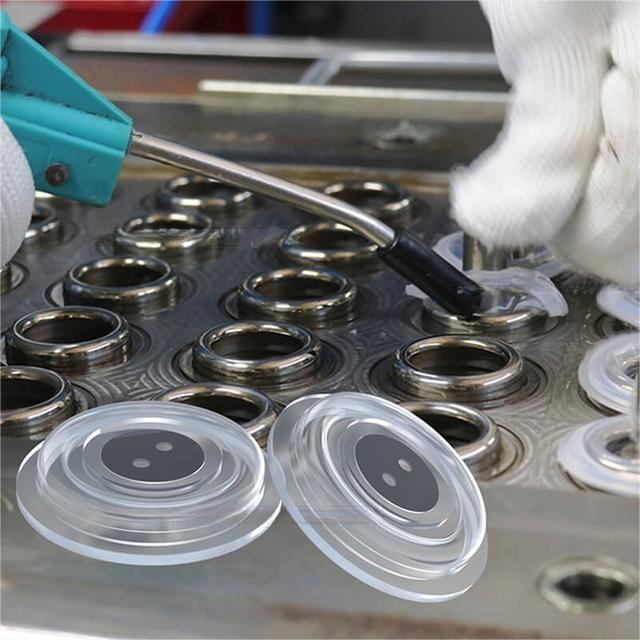
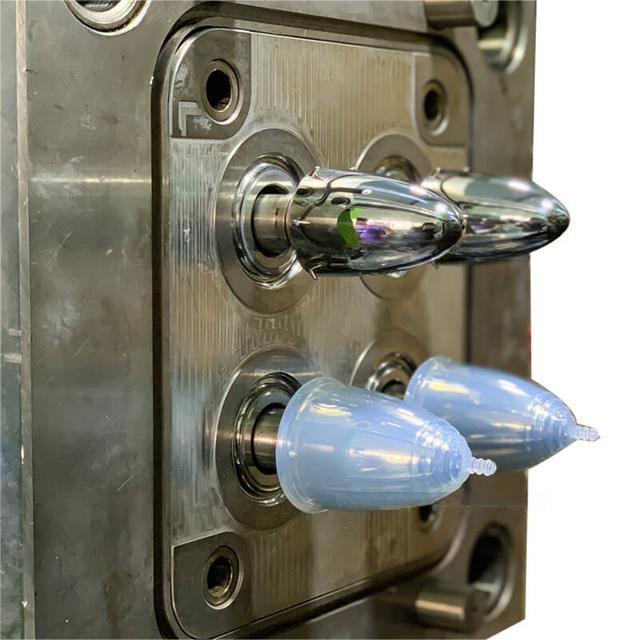

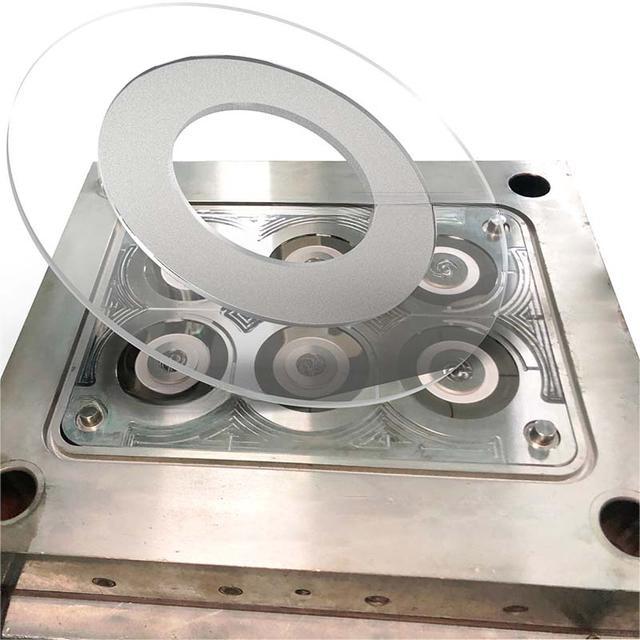
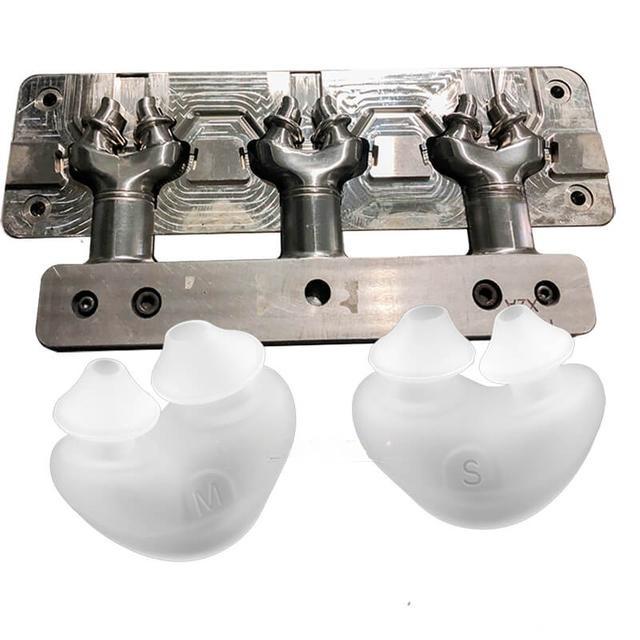

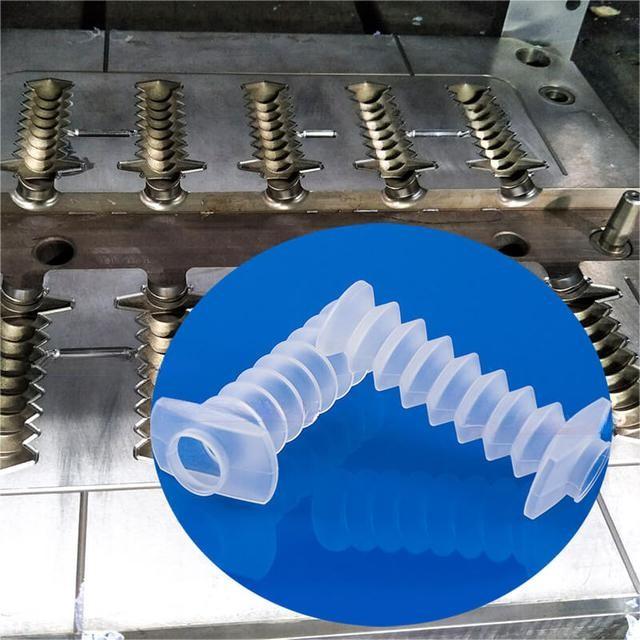
The Silicone Moulding Production Process
All phases of the silicone product development process, including product design, precision tooling, manufacturing, and fulfillment, take place at LGDSilicone under one roof.
1. Select the appropriate durometer and silicone material

We can recommend the optimum silicone material by properly assessing the needs of our customers. The most practical material will be chosen based on the product’s structure and function, the application environment, performance, safety test requirements, and the customer’s budget.
2. Silicone material compounding and blending

3. Cutting / Blanking
Silicone material after blending will be collected in large rolls covered with film to prevent dust or dirt. It then will be cut into slices by an automatic cut machine. The slices’ length and width will be controlled according to the silicone part’s weight to be molded. Silicone blanking makes it easier for our molding operators to weight the material during silicone molding production.
4. Put the silicone substance on the hot tool mold and weigh it down.

5. Silicone part vulcanization molding
Silicone material will be fully cured under high temperature and pressure from vulcanizing molding machine, then the silicone parts are formed. Our molding department is equiped with 8 high precision automatic vacuum vulcanizing machines which can be used to craft more high performance silicone parts. Our sophisticated molding machines, coupled with our skilled operators, provide the capacity and flexibility to mould high-quality, high-volume silicone parts in short peroid.
6. Demolding
The vulcanizing molding machine will automatically relieve pressure after the silicone is fully cured, allowing molding personnel to remove the silicone-molded pieces by pulling out the tool mold. The raw material will be repositioned for the following vulcanization cycle.
7. Deflash
Silicone Flash – Is a thin flap of material at the parting line where the mold splits. Due to the low viscosity of silicone material and high molding pressure during heating and curing, The pressurized silicone material will flow to every spaces of tool mold. Flash can be minimized with favorable designs and better tooling and accurate material weight during vulcanizer molding production. Flash will be removed mainly by hands, cryogenics deflashing can also be applicated for some cases.
Where do you find silicone parts?
LDGSilicone supplies a wide range of custom Silicone Rubber molding parts. These parts can be found in products used in a wide array of industries, including automotive, Aerospace,Cookware, life sciences (such as medical/healthcare /baby care products), and Toy and special applications.
The Measurement Center
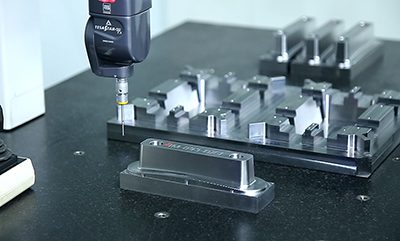
3D Measurement System
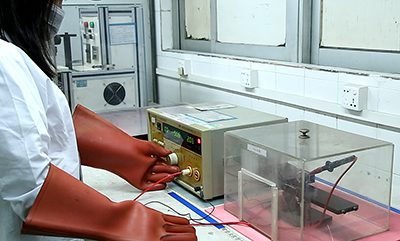
Insulation Test
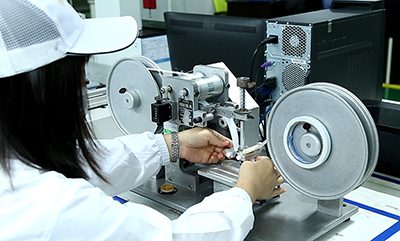
RCA Abrasion
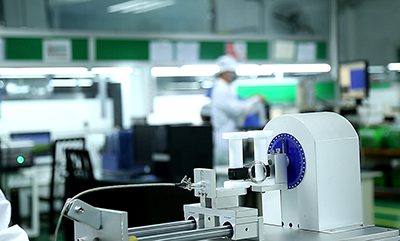
Torque Test

Tensile Test
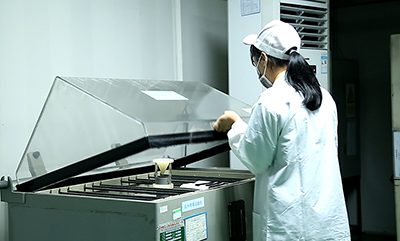
Corrosion Test

H-L Temperature Test
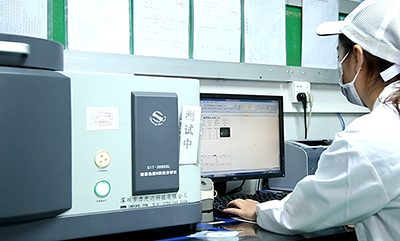
XRF Test for RoHS
Custom Silicone Mold FAQs
What equipment is needed for injection molding?
- 5 years of plastics injection molding set-up and processing experience
- Experience with robotic load/unload/packing equipment is highly preferred
- Hand-on set-up related experience with plastic injection molding machines, cranes, various hand tools, temperature controllers, drill press, tapping arms, pick and place robots, etc.
Can You injection mold silicone?
Injection molding of liquid silicone rubber is a process to produce pliable, durable parts in high volume. Liquid silicone rubber is a high purity platinum cured silicone with low compression set, great stability and ability to resist extreme temperatures of heat and cold ideally suitable for production of parts, where high quality is a must. Due to the thermosetting nature of the material, liquid silicone injection molding requires special treatment,
What is made by injection molding?
How much does a silicone mold cost?
The cost of a silicone mold or tool depends on the requirements of your product. Before you can get pricing, you must have an engineered design. Laminar Industries can help streamline the quote for you. Pleas contact us at sales@lgdsilicone.com and we’ll be happy to help point you in the right direction.