Liquid Silicone Rubber Injection Molding Manufacturer
LGDSilicone Parts is a leading provider of produced parts using the Liquid Silicone Rubber Injection Molding. Our advanced production capabilities, outstanding quality and two decades of experience with silicone rubber components make us an ideal partner for your next project.
What Is Liquid Silicone Rubber?
Liquid silicone rubber (LSR) is a two-part silicone-based polymer joined together by a chemical bond.
liquid silicone rubber injected Molding is a high purity platinum cured silicone with a low compression set, great stability, and capability to tolerate exceptionally high and low temperatures in order to make components of the finest quality.
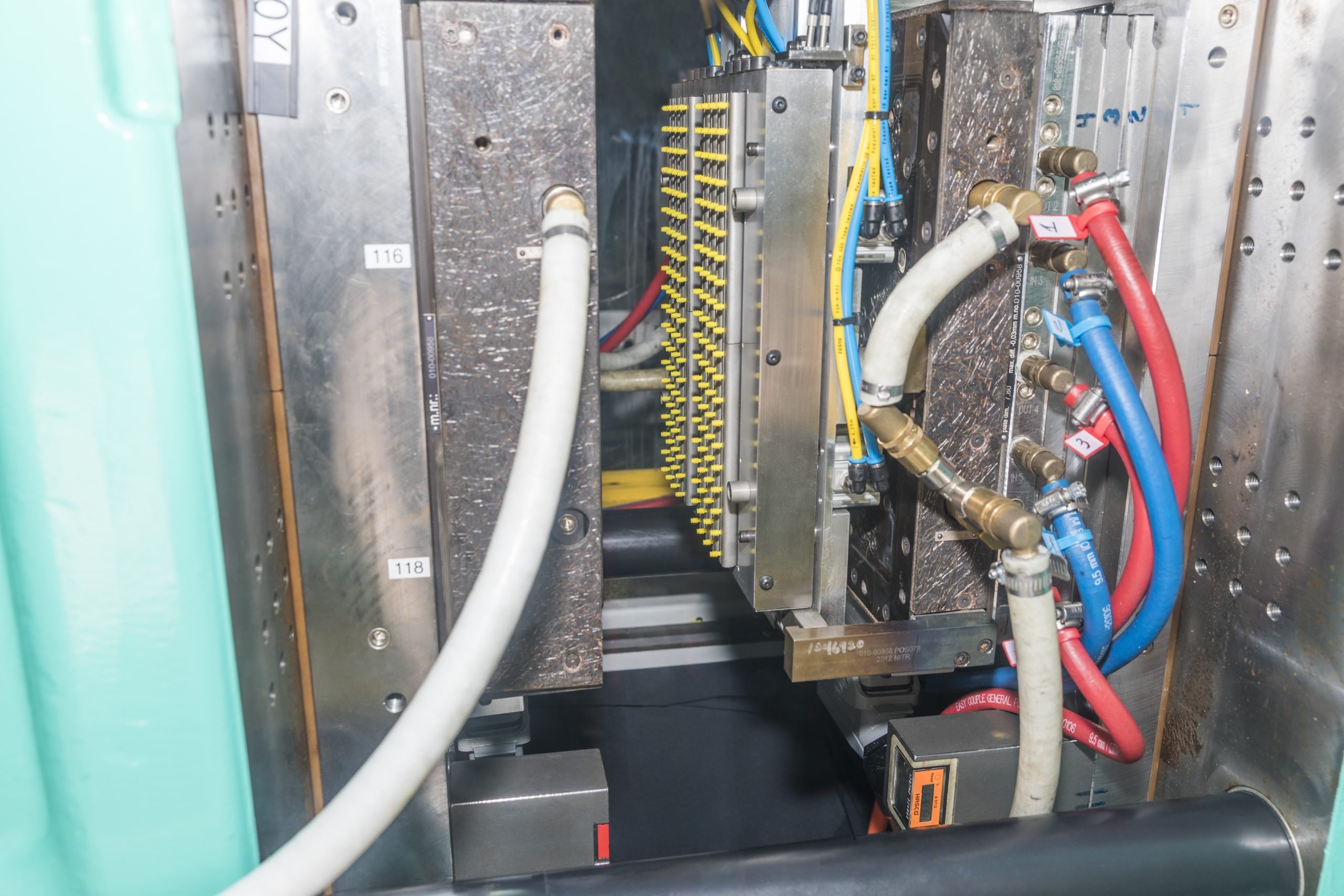
Features of LSR Injection Molding
Liquid silicone rubber is high-purity platinum cured silicone. LSR rubber is ideally suited for goods where performance, durability, and high quality are requirements because to its physical, chemical, and thermal qualities.
In addition to being resistant to damage from water, oxidation, UV rays, ozone, and radiation, liquid silicone rubber does not react with chemical products that are alkaline or acidic.
Even among people with sensitive skin, LSR’s inherent hypoallergenic and non-toxic properties mean that contact with it won’t result in irritation or allergic responses.
Liquid silicone rubber is compliant with the Food and Drug Administration (FDA), has no taste, and has no odor.
When compressed, LSR parts will maintain their shape.
For standard grades, offers excellent stability in temperatures ranging from -40 degrees Fahrenheit to -392 degrees Fahrenheit (-40 degrees Celsius to 200 degrees Celsius).
For molding precise, fragile components, LSR liquid injection molding is the technique of choice. These substances can act as conductors or insulators, depending on their chemical make-up.
The LSR injection molding Process
High-purity platinum cured silicone is what makes up liquid silicone rubber. LSR is ideally suited for goods where performance, durability, and high quality are requirements because to its physical, chemical, and thermal qualities.
- 1.Material enters the barrel
- 2.Material melts and mixes
- 3.Volume of material (Shot sizes in barrel is created)
- 4.Mold closes
- 5.Injection of the silicone into the mold cavity
- 6.Molten material cooled (during this process, steps 1-3 are preparing for next cycle)
- 7.Mold opens and Part ejects
- 8.Return to Step 4 for the next cycle
Advantages of Lgdsilicone’s LSR Injection Molding
Liquid silicone rubber is high-purity platinum cured silicone. LSR’s physical, chemical and thermal properties make it highly suitable for products where performance, durability and high quality are a necessity.
Batches stability
Short cycle time
Process repeatability
Automated process
Direct injection No waste
Automated demolding systems
Industries and Applications
LDGSilicone supplies a wide range of custom Silicone Rubber molding parts. These parts can be found in products used in a wide array of industries, including automotive, Aerospace,Cookware, life sciences (such as medical/healthcare /baby care products), and Toy and special applications.
LSR Injection Molded Production Capabilities
LGDSilicone offers several options for LSR part production
- Single-shot molding: In this molding process, only one LSR material is used for injection molding parts.
- Multi-shot molding: For more complicated components, LSR is integrated with two or more polymers or a polymer plus substrate.
- Overmolding: Overmolding involves molding liquid silicone rubber around a substrate or completed product.
- Micromolding: Small, intricate pieces are produced using this injection molding technique, often with a shot weight of under 1 gram.
- Hygienic molding: LSR parts are manufactured in a sterile, hygienic setting that is strictly regulated to a number of levels, such as white rooms ISO cleanrooms with different classes.
Custom Silicone Injection Molded FAQs
The main steps in the liquid silicone rubber injection molding process are as follows:
1 Two containers, Compound A and Compound B, which are connected to the pumping system, hold the liquid silicone that has not yet hardened.
2 The automated injection molding machine may be programmed and customized by the molder, and the injection setting can be changed.
Liquid injection molding (LIM) is a method used in industrial manufacturing to shape materials into a variety of parts and goods. Liquid injection molding uses a mechanical mixing technique that primarily concentrates on liquid silicone rubber (LSR) and related elastomeric materials, in contrast to the typical reaction injection molding process, which depends on pressurized impingement mixing.
When the qualities of LSR are combined with the hygienic liquid injection molding manufacturing method, the end product has higher resilience and performance. LSR is a thick liquid polymer that is produced using a clean liquid injection molding technique to create components.
Polysiloxane, sometimes referred to as silicone rubber in science, is an elastomer consisting of silicon, carbon, hydrogen, and oxygen. It is safe to use for infant bottle teats and tough enough to withstand the rigors of jet engines. High-performance polymer made from silicon metal and silica powder is known as silicone rubber.
Silicone Rubber Molding Other Production Capabilities
LGDSilicone offers several options for Silicone Rubber Molding Production Capabilities
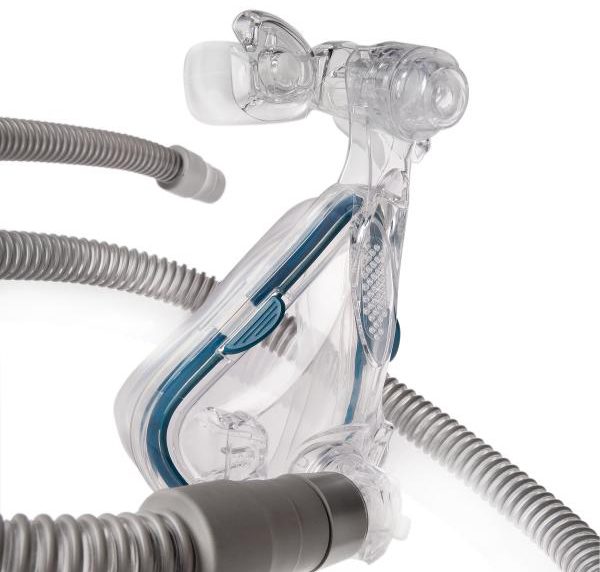
Silicone Overmolding
Silicone over-molding involves placing a metal or plastic part into a mold cavity and heating it to cure it

Compression Molding
Silicone Rubber Compressing Molding is the process of Compression Molding with Silicone Rubber as the material.

Silicone Extrusion
Silicone extrusion is the process in which silicone is forced through a shaped die in to produce a continuous formed length

Silicone Calendering
Silicone calendering is a mechanical process used to manufacture uniform sheets made of silicone rubber