The valve gate injection molding process is a successful and frequently used method for producing silicone parts in large quantities that need to be of the highest quality, such as medical and aesthetic parts. This is due to the problem of traditional injection molding, which is that silicone tends to flow off as it is shot out of the nozzle of the injection barrel. This flaw could not only detract from the item's look but also from its general strength and quality. Therefore, a technique for avoiding this drooling effect should be used; here, valve gates are useful.
The primary purpose of valve gates, a particular kind of hot runner gate with a distinctive gate pin or valve, is to regulate the flow of silicone into the mold. Everything you need to know about valve gating systems, from their definition to their uses and benefits, will be covered in this article.
What is a valve gate injection molding
A mechanical system called a valve gate system is used to mechanically open and close the gate that allows molten silicone to be released from an injection molding machine into a tool.
The great majority of hot runner systems on the market are still thermally driven, despite the fact that valve gate systems offer the best aesthetic gate performance and are required to stop molten silicone from drooling during vertical injection molding operations.
The initial cost will typically be the deciding element when choosing a thermal gate, and frequently the molder will sacrifice the process advantages that may be gained by using valve gate designs.

Types Of Gating For Injection Molding
Selecting the appropriate gate is an important part of mold design. The idea behind the gate's operation is straightforward, however picking the incorrect kind of gating might result in a number of issues with processing. We'll talk about a variety of gate designs and their applications in this post.
EDGE GATE

Edge gates are frequently utilized in the injection molding process due to their efficiency and simplicity. When creating a mold, they are simple to make and, if necessary, may be adjusted. They are also perfect for filling larger spaces or areas where it was impossible to avoid using thicker wall panels. Compared to conventional gates, an edge gate may have a higher cross-sectional area. Due to the prolonged gate freeze, this enables more silicone flow and longer hold lengths.
TUNNEL / SUBMARINE GATE

You should configure the system to automatically trim the tunnel gate while utilizing it. Additionally, it works well for tasks requiring the creation of tiny silicone components. However, to prevent problems like shear stress or cracking, you require production experience. You could have trouble filling the mold because this gate is smaller in size.
CASHEW GATE

The cashew gate is machined below the separating line and is mechanically sheared upon ejection, much like a tunnel gate. Using this type of gate, the injection spot can be reached beneath or below a display surface. The size restrictions on cashew gates are frequently the same as those on tunnel gates.
Hot Runner – Thermal Gate
Compared to cold runner systems, hot runner feed systems have various benefits. Here is additional information about this. Between the molding machine barrel and the part, hot runner systems are made to keep the molding material molten (In some cases, there are short cold runner systems added after the hot runner). There are primarily two types of gates utilized at that period.

Hot Runner – Valve Gate
While adding an additional layer of control, the valve gated hot runner system offers the same benefits as the hot runner thermal gate. Inside the hot runner tip assembly in this style is a moveable pin. Molten silicone can pour into the cavity when positioned back (left side of the figure below). silicone flow is stopped when moving forward (right side of the illustration below). This offers greater gate sizes, improved runner feed system management, and less gate vestige.
Design Considerations For Injection Molding Gate
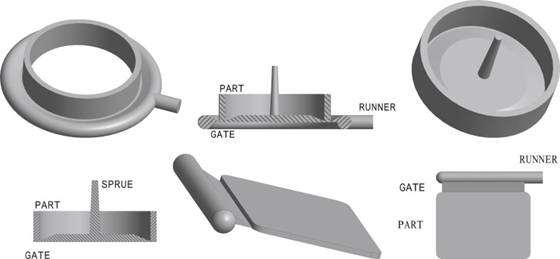
Distinct injection molding gates use different processes for molding diverse components. Here are some crucial aspects to bear in mind when you decide between these designs:
Gate Placement
The positioning of certain gates makes it more challenging to separate them than others. The placement of particular gates can also cause deformities and lines in molded components. As a result, you need to be careful when placing the gate in your injection molding design.
Gate Size
When using injection molding, the gate size must allow for correct shearing each time the mold is fed through the apparatus. The gate's proportions must permit proper mold filling. High shear heating rates are present in smaller gates. However, if they are either too little or too huge, they may unintentionally increase flow pressure. Use gates that are the right size to achieve the greatest outcomes.
Part Shape and Finish
For molding pieces with various forms and a particular finish, each gate design is advised. For instance, the cashew gate design delivers a clean and consistent surface finish and is perfect for processing tiny parts.
Why Use an Injection Molding Valve Gate?
Shortly after the first hot runner systems hit the market, the injection molding industry received valve gate hot runner nozzles. Valve gates have traditionally been used in circumstances where thermal gate vestige is undesirable. However, valve gates provide the injection molder with a number of extra component quality and production advantages, such as:
- Elimination of gate string and drool.
- reduced molded-in stress and improved physical characteristics.
- decrease in cycle time.
- Ability to use sequential valve gating to balance family molds and regulate the position of weld lines.
- improved molding techniques for thin-walled components.
What is open gate vs valve gate?
In an open gate technique, molten silicone is immediately injected into the mold cavity, leaving a few minute ridges on the finished product. A valve pin is used in a valve gate system to open and close the hot runner nozzle, preventing the melted silicone from stringing and drizzling at the tip.
What is the difference between fan gate and edge gate?
Edge gates and fan gates both require manual degating and are affixed to the component at the separating line. The fan gate, in contrast to the edge gate, extends in the shape of a fan from the runner, with its widest end opening to the hollow. The fan region, which may be rather dense, feeds a sparse gate land.
How to Use a Valve Gate
The liquid silicone would continue to flow out even after the injection mold is filled in the absence of a valve gate. This results in the silicone strand hanging from the mold to the nozzle, leaving a bit of the tag hanging from the completed object when the silicone has dried and hardened. A valve gate is utilized to rapidly stop any form of flow of silicone out the nozzle in order to prevent this kind of dripping effect. The amount of silicone required to fill the mold is programmed into the injection molding. The valve gate instantaneously closes after this exact volume of silicone has exited the injection molding machine's barrel and out the nozzle, obstructing the passage of any further silicone . There is no silicone left over to produce the hanging silicone tag since the silicone flow is stopped exactly where the valve is located.
Where do you put the gate on injection molding?
To guarantee the optimal flow, minimize voids, and prevent sinking, gates should be put at the deepest cross-section. The gate should be placed on one side of the mold so that the function won't be compromised by the stress and deformation of the runners and the gate.
Conclusion
Despite being more expensive than thermal gates, valve gates provide excellent value. Valve gate nozzles may boost production and enhance component quality in addition to providing outstanding gate quality. When deciding if a valve gate nozzle is suitable for your mold, you need carefully analyze all of the advantages, not simply gate quality alone. To make sure the correct nozzle design is utilized in your mold, valve gate applications should also be discussed with your hot runner provider.