This guide provides comprehensive information on thermoplastic elastomers, covering their properties, features, applications, and classification criteria. Whether you are interested in any of these topics, you can find all the information you need right here.
Thermoplastic Elastomer Meaning
Thermoplastic elastomers (TPEs), also known as thermoplastic rubbers (TPR), are a type of copolymer or a physical mix of polymers (typically a plastic and a rubber) that have both thermoplastic and elastomeric qualities.
While most elastomers are thermosets, thermoplastics are comparatively simple to employ in production, such as injection molding. These can also be recycled! These polymers are exceptionally robust and can be repeatedly stretched to at least twice their initial length with complete quick recovery, but they are genuine thermoplastics and do not require curing or vulcanization like other rubbers.
How Are Thermoplastic Elastomers (TPEs) Made?
Chemical techniques such as graft or chain copolymerization are used to create thermoplastic elastomers. Copolymerization of two or more monomers is used in these. One monomer produces hard crystalline segments, while the other forms an amorphous or soft segment, giving the material its elastomeric character. The following are descriptions of the two copolymerization techniques:
- Block copolymerization produces a polymer backbone composed of repeated blocks of hard and soft segments.
- Graft polymerization is the process of joining polymer chains as branches to a polymer backbone. Because the branches and backbone may have variable degrees of hard and soft parts, this approach allows for greater personalization.
7 Uses of Thermoplastic Elastomers
Uses of thermoplastic elastomers vary between industries. It’s important to pick a TPE material that is compatible with the application where it will be used.
Uses of TPE | Description |
---|---|
Automotive | TPE is used for automotive applications due to its flexibility, excellent wear, chemical, and electrical resistance, and UV stability. |
Construction | TPE’s durability and flexibility make it the perfect choice for extruded weather seals. |
Industrial | TPE has excellent damping ability for applications such as anti-vibration mounts and springs. |
Consumer Products | TPE’s durability, flexibility, ease of molding, and chemical resistance are desirable for remote control covers and mobile phone cases. |
Medical | TPE is flexible, biocompatible, lightweight, and chemically resilient. This makes it useful for breathing tubes, syringe seals, masks, and other airtight seals. |
Electronics | TPE is used for mobile phone components, cables, plugs, and sockets due to its electrical resistance and ability to be molded. |
Sporting Goods | TPE is used for shoe soles, scuba flippers, and ski pole handles due to its flexibility, wear resistance, and UV stability. |
Table: Common Applications and Uses of TPE Material
Types of Thermoplastic Elastomers (TPEs)
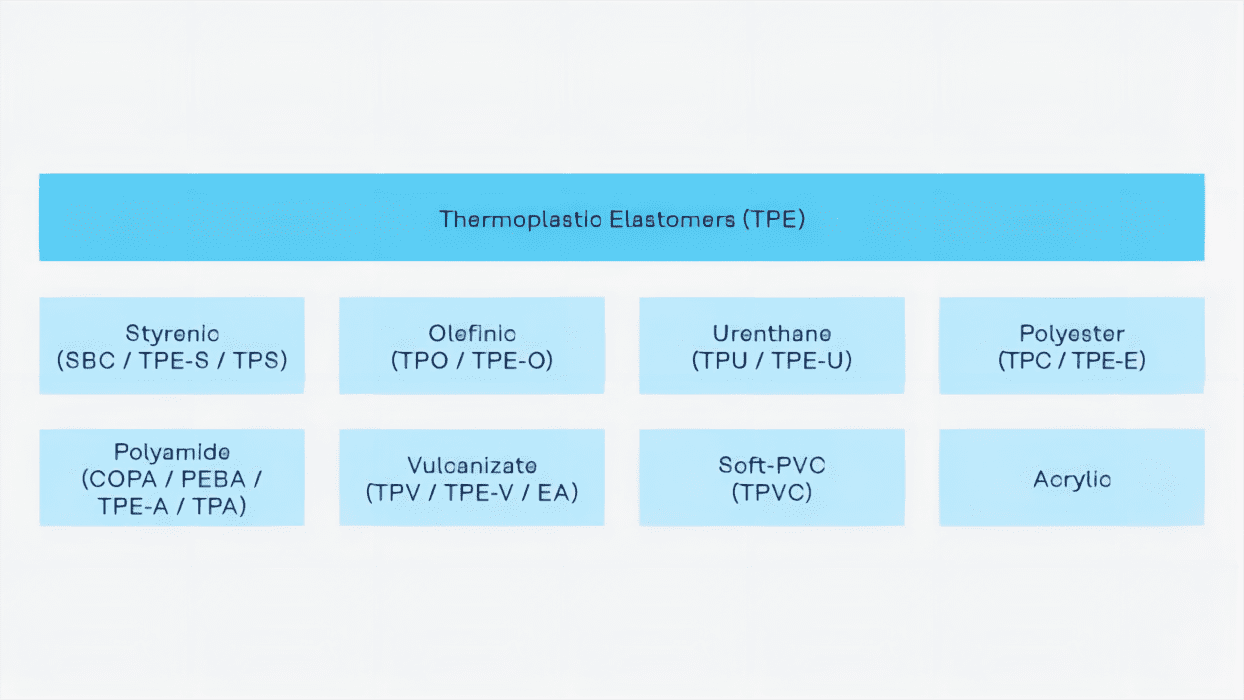
Types of TPEs | Definition | Typical Uses |
---|---|---|
Styrenic Block Copolymers (TPE-S) | Molecular structure consists of repeated styrene and butadiene units with styrene end caps. | FootwearAdhesives |
Thermoplastic Polyolefins (TPE-O or TPO) | A blend of polypropylene or polyethylene and another elastomer. | Automotive bumpersDashboardsAirbag coversMudguards |
Thermoplastic Vulcanisates (TPE-V or TPV) | Made from a mixture of polypropylene and EPDM that is vulcanized during compounding. | Automotive sealsBellowsHosesPipe seals |
Thermoplastic Polyurethanes (TPE-U or TPU) | Formed by reacting diisocyanates with either a polyester or polyether polyol. | Caster wheelsPower tool gripsHoses & tubesDrive belts |
Thermoplastic Copolyesters (TPE-E or COPE or TEEE) | High-performance thermoplastic elastomers | Vehicle air ductsVentilator bagsDust bootsConveyor belts |
Melt Processable Rubber (MPR) | An alternative to vulcanized rubber that consists of a cross-linked halogenated polyolefin mixed with plasticizers and stabilizers. | Automotive weather stripsInflatable boatsSealsGoggles |
Thermoplastic Polyether Block Amides (TPE-A) | Consists of soft segments made from either polyethers or polyesters and hard segments made from polyamide. | Aerospace componentsCable jacketing |
Table 1. Types of Thermoplastic Elastomers
9 Advantages of Using Thermoplastic Elastomers
This explains the advantages of using thermoplastic elastomers.
1.Thermoplastic Elastomers Provide a Wide Range of Applications
Thermoplastic elastomers are extremely adaptable. This implies that TPE may be easily customized during the production process to better fit the product’s final usage and environment. TPE tubing, for example, can range from soft and jelly-like to stiff and unyielding. TPE goods can also be manufactured in a variety of bespoke sizes.
2.TPE (thermoplastic elastomer) is naturally chemical resistant and can be flame retardant.
Thermoplastic elastomer is chemically resistant by nature. It is also possible for it to be flame retardant. TPE products offer outstanding chemical characteristics and stability as a consequence, even when subjected to a wide variety of temperatures and environmental variables. Because TPE is chemically resistant, it improves the quality and durability of the final TPE product.
3. Thermoplastic elastomer materials require little to no compounding and do not require any reinforcing agents, stabilizers, or curing systems.
Thermoplastic elastomers do not require much compounding and do not require reinforcing chemicals, stabilizers, or cure systems. There is essentially little difference across batches with weighing and metering components due to the lack of compounding. The absence of variance enhances the uniformity of raw materials and finished products. TPE’s consistency makes it a desirable alternative to rubber or plastic in some applications.
4. Thermoplastic elastomers are an excellent environmentally friendly choice.
Since they are recyclable, thermoplastic elastomers are considered ecologically friendly. Non-toxic, recyclable polymers may be used to create TPE materials. TPE production uses less energy than other materials and is frequently recyclable through molding or extrusion. TPE may be recycled in a variety of ways. One alternative is to shred it and use it as a filler in other goods. Another option is to melt it down and make new items from it.
5. Thermoplastic elastomers are naturally latex-free and hence safe for those who are latex sensitive or allergic.
Thermoplastic elastomers are latex-free by nature. Many rubber items include latex, which causes allergic reactions in certain people. TPE, depending on how it’s produced, may be soft to the touch, making it a suitable choice for healthcare devices that come into direct contact with patients since that pleasant feel can make a difference in the patient’s comfort. TPE is also simple to sanitize, making it useful in healthcare and the food and beverage industries.
6. Thermoplastic elastomers can be a cost-effective and efficient alternative to other materials.
Thermoplastic elastomers are considered cost-effective since they need less energy to manufacture. TPE requires less processing and has quicker production periods than other materials, which can result in significant cost savings. As a result, TPE can be a more efficient and cost-effective material than natural rubber latex, silicone, and polyvinyl chloride compounds.
7. Thermoplastic elastomers are an excellent material for large-scale injection molding and extrusion.
Thermoplastic elastomers are useful for injection molding because one of their distinguishing features is their ability to be processed as a melt at extreme temperatures. Since injection molding necessitates these properties, TPE works well with both high-volume injection molding and extrusion.
8. Thermoplastic elastomers are color and dye resistant.
Color and dyeing thermoplastic elastomers are simple. Moreover, TPE may be tailored to fit a wide range of colors and finishes, including fluorescents. It has high clarity, which makes it suitable for medical tubing and other uses.
9. Thermoplastic Elastomers Are Useful in a Variety of Situations
Thermoplastic elastomers are employed in a wide range of applications. TPE has been increasing in popularity for several decades. Several sectors are continually exploring new and novel ways to employ TPE because of its numerous benefits in material and performance features.
What Are the Disadvantages of Thermoplastic Elastomers (TPEs)?
Despite their great thermoplastic elastomer qualities, TPEs have some significant drawbacks, which are noted below:
- TPEs are hygroscopic, which means they collect moisture and must be well-dried before use.
- Melting: Since TPEs have a low melting point, they can be melt-processed using normal thermoplastic processes. TPEs, on the other hand, can be irreversibly destroyed if heated over the breakdown temperature of the polymer’s soft segments. As a result, their high-temperature uses are limited.
- TPEs are often tougher than other elastomers such as rubber or polyurethane. This is owing in part to the polymer’s incorporation of thermoplastic hard segments. Hardnesses of 80 Shore A and above are usual.
Thermoplastic Elastomer (TPE) processing
Injection molding
By far the most essential technique for processing TPE material is injection molding. The fundamental reason for this is injection molding’s high productivity and clean, residue-free processes.
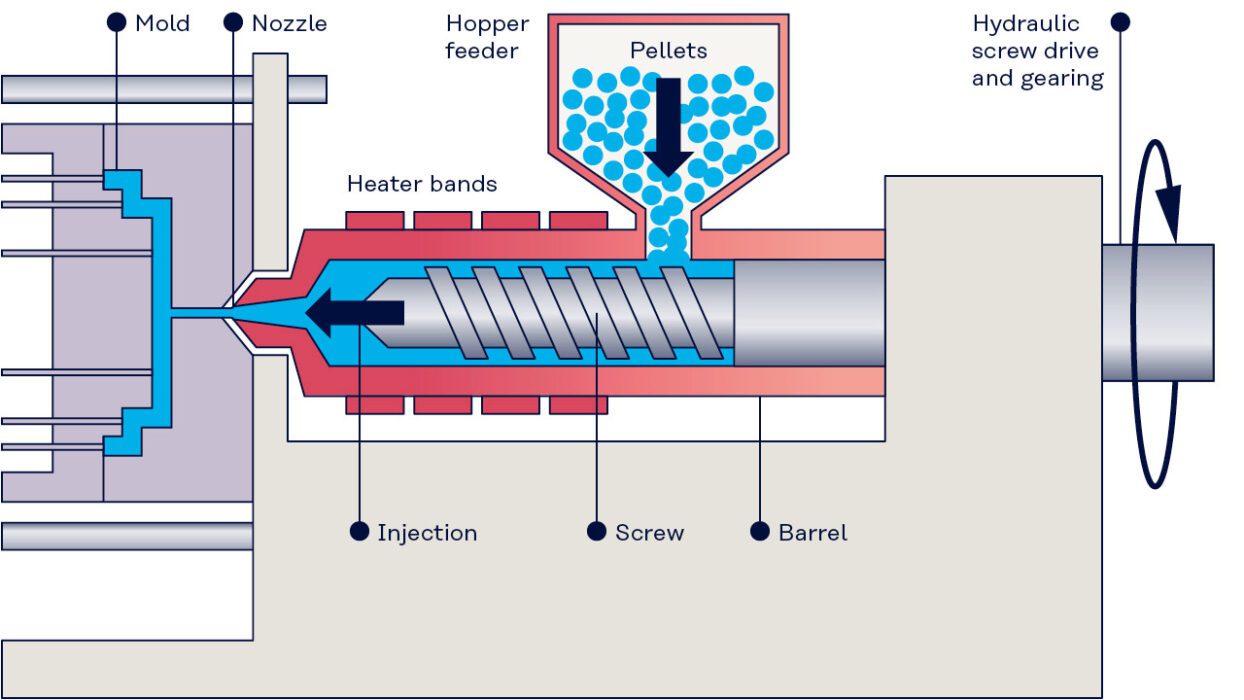
In injection molding, molten plastic is injected into a mold, creating an identical replica of the mold. TPEs behave similarly to other thermoplastics in the hot runner in this procedure. The co-injection and insert-injection techniques are both appropriate for this application. Injection molding is mostly used to make solid things, such as tools or components, in huge numbers and with high precision.
Extrusion
Extrusion is a popular method for producing tubes, profiles, and other thermoplastic elastomer products. The material is molded in this continuous process by driving it through a die with a cross-sectional profile that the substance adopts.
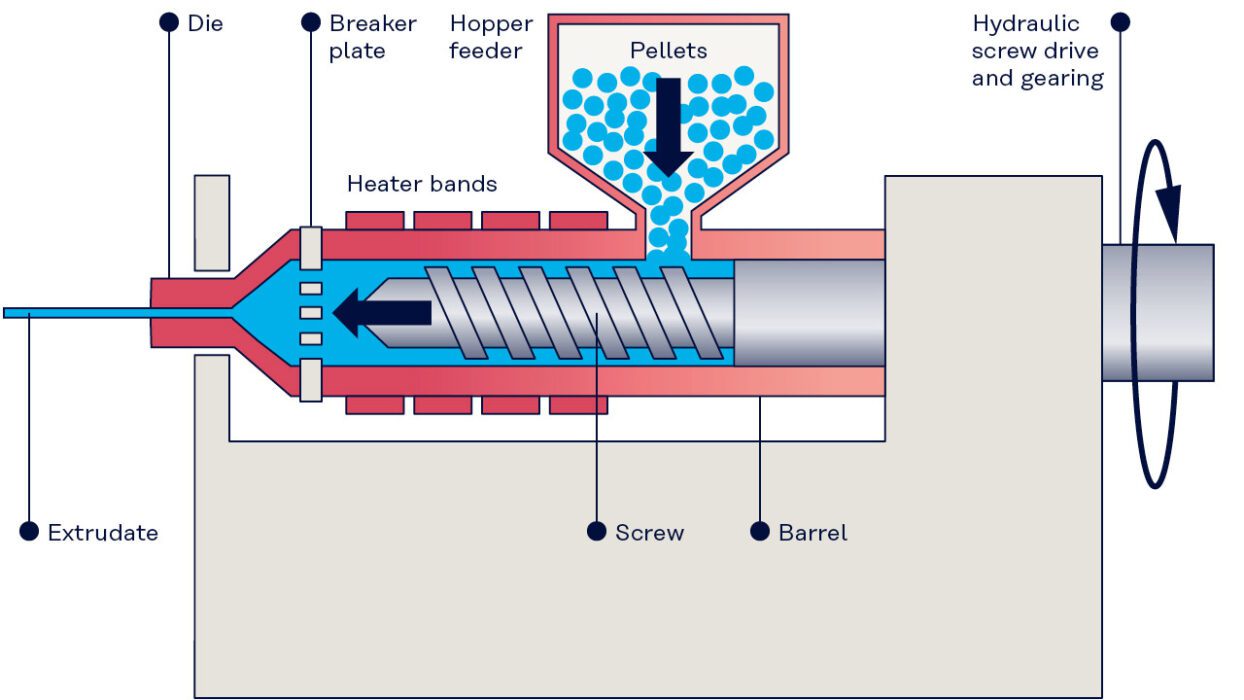
TPE pellets are fed into the extruder’s hopper and then heated and melted by a spiral screw revolving in a heated barrel. The screw forces molten plastic through a die to form continuous lengths of molds with the same profile, which are subsequently cooled. Unlike injection molding, extrusion typically produces a semi-finished or intermediate product that must be further treated. This technology may be utilized to create exceedingly complicated cross-sections with a very good surface polish and a great degree of design freedom.
Extrusion blow molding
TPE extrusion is another significant procedure for shaping profiles. Molten plastic is extruded into a mold or die in extrusion. The required form is subsequently created by blowing air into the mold or tool.
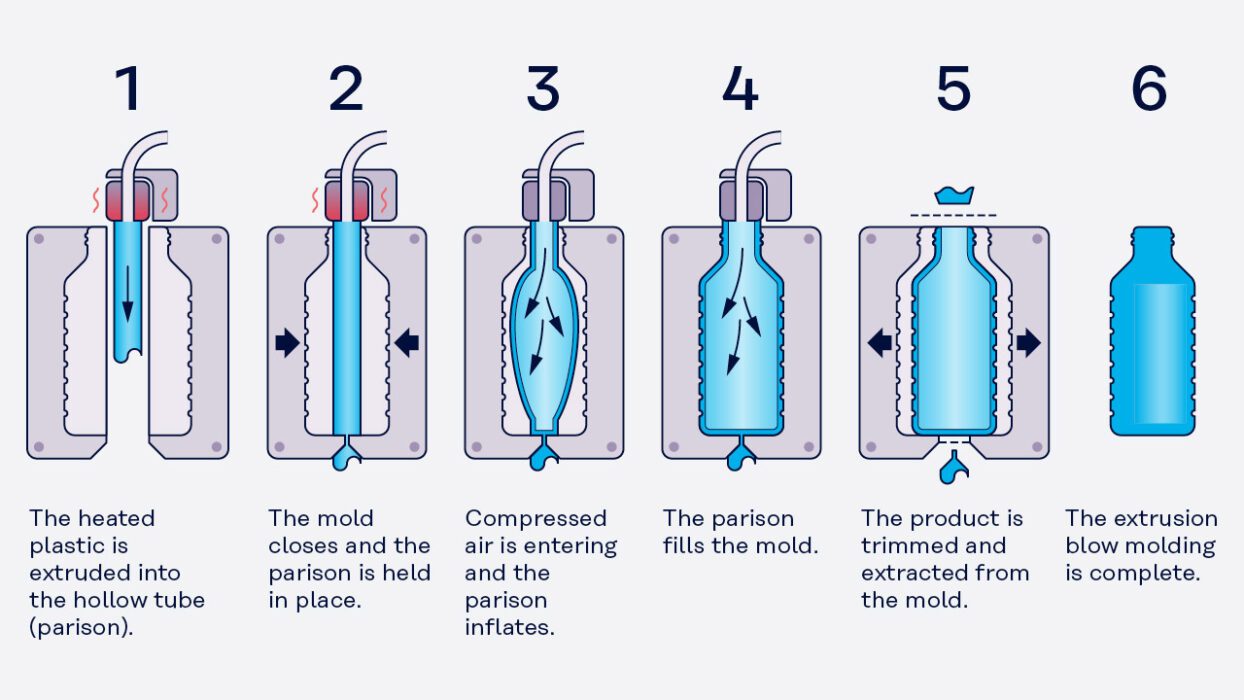
The single-screw extruder is the leading technology here. Other extruders, such as triple-screw extruders, are utilized as well. Extrusion is used to make intricate hollow objects like bottles and containers. Extrusion is used to make sheets, pipelines, and other forms in addition to profiles.
Thermoplastic Elastomer FAQs
Is thermoplastic elastomer safe?
People also ask whether TPEs are safe. Absolutely, they are safe enough to use in the production of sippy cups and healthcare items such as medical tubing. TPEs can also be designed for fire retardant performance if required for the application. The material is non-allergenic and does not cause skin irritation.
Are TPEs waterproof?
TPEs can be combined in such a way that the material becomes completely waterproof. TPEs are frequently utilized as the gasket that protects portable speakers and other electronics from water damage. TPEs, on the other hand, can be tailored to absorb water if that is a desirable feature for your application.
Is thermoplastic elastomer a rubber?
TPEs are a class of rubber-like materials that combine the properties of rubber with the recyclability and processing benefits of plastics.
Is thermoplastic elastomer like silicone?
TPE, or thermoplastic elastomer, and silicone are two rubber compounds that are comparable in many ways. Both are often utilized in the injection molding process. Silicone has a distinct behavior at high temperatures and lacks a melting point, remaining solid until combustion occurs. At high temperatures (200-450°C), silicone rubber gradually loses mechanical characteristics and becomes brittle. TPE has a melting point of 260-320 degrees Celsius.
For more information as our guide on Thermoplastic Elastomer vs Liquid Silicone Rubber
Summary
This article discussed Thermoplastic Elastomer materials, including their kinds, uses, applications, manufacturing techniques, and toxicity. Contact one of our application engineers or material specialists for additional information on the many thermoplastic elastomers applications and how to effectively use TPE material to meet your specific needs.